Riduzione dei costi nella pressofusione di zinco
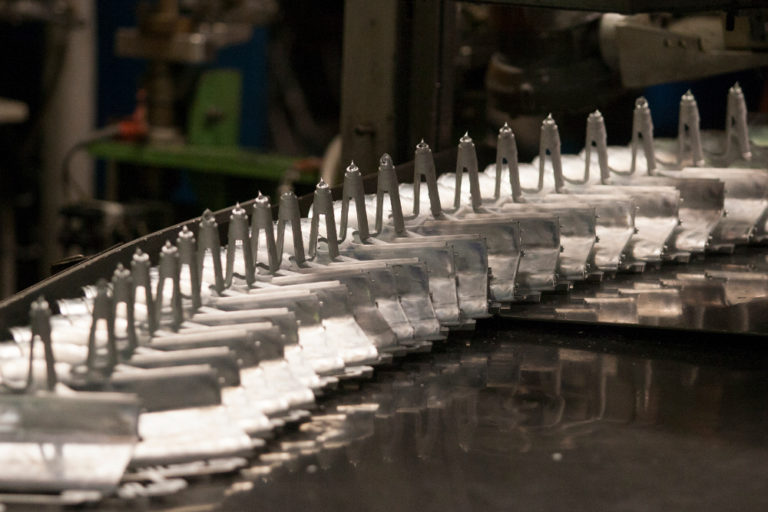
La riduzione dei costi nella pressofusione è un’attività che deve essere eseguita senza inficiare la qualità e la funzionalità del componente prodotto. Tutte le attività volte ad aumentare la produttività, diminuire gli scarti e semplificare i processi produttivi sono strategie di riduzione dei costi, così come lo sono le scelte fatte a livello di materiali e di lavorazioni.
Strategie di riduzione dei costi nella pressofusione di zinco
La riduzione dei costi nella pressofusione di zinco può essere attuata a diversi livelli. Lo zinco, infatti, è un metallo versatile che, se lavorato con le giuste tecnologie, permette di risparmiare sia in termini assoluti, riducendo il tempo, l’energia e la quantità di materia prima utilizzati nei processi produttivi, sia relativamente ad altri metalli.
Nella produzione di pressofusi è quindi possibile attuare una riduzione di costi:
- Scegliendo lo zinco al posto di altri metalli o di altre leghe metalliche
- Ottimizzando il processo produttivo
- Progettando processi e componenti assieme al cliente attraverso metodologie di co-design
Vantaggi dello zinco: qualità e caratteristiche chimico-fisiche, temperatura di fusione, economia circolare
Le leghe di zinco comunemente usate nel processo di pressofusione hanno proprietà che le rendono competitive rispetto ad altri metalli. Queste proprietà, di natura chimico-fisica, permettono di ottenere una riduzione dei costi relativa sia ai processi di produzione sia alle fasi successive, come ad esempio quelle di smaltimento e di riciclo. Analizziamole più nel dettaglio.
Qualità e caratteristiche chimico-fisiche
Nel processo di pressofusione sono impiegate diverse leghe di zinco, le più comuni sono Zamak 2, 3 e 5. Queste leghe, per la realizzazione dei diversi prodotti, sono scelte in funzione delle loro proprietà chimico-fisiche. Infatti, a seconda delle percentuali e dei valori relativi dei metalli che contengono assumono diverse caratteristiche che le rendono più o meno adatte alla realizzazione di determinate tipologie di componenti. Se, per esempio, il componente da realizzare è un componente di sicurezza si privilegia la lega in grado di offrire maggiori resistenza ad usura, corrosione e pressione, sopportazione del carico di snervamento e stabilità dimensionale. Nel caso di componenti tecnici, invece, per i quali è spesso importante ottenere dettagli e sottili nervature, la Zamak da preferire sarà quella più fluida, in grado di riversarsi nello stampo con la maggiore uniformità possibile. In questo modo sarà infatti possibile ottenere spessori sottili, determinanti per garantire la funzionalità dei prodotti. Per i prodotti estetici, infine, sono preferibili le qualità di Zamak in grado di assicurare la migliore qualità superficiale e la migliore resa se sottoposte a lavorazioni successive e finiture. È quindi importante conoscere le caratteristiche fisico-chimiche delle diverse leghe di zinco per poter scegliere quella più appropriata alla realizzazione di uno specifico componente. Solo così, infatti, sarà possibile fare una scelta vincente e ottenere, con percentuali di scarto ridotte, pressofusi di qualità e che necessitano di un numero ridotto di finiture e lavorazioni ulteriori.
Per scoprire di più sulle diverse leghe di zinco e su come sfruttare al meglio le loro diverse caratteristiche puoi leggere gli articoli Le migliori leghe di zinco per la pressofusione a camera calda e Composizione della Zamak per pressofusione.
Se invece desideri approfondire i vantaggi dello zinco rispetto ad altri metalli leggi L’importanza della pressofusione nel settore automobilistico e Vernici, placcature e altri tipi di rivestimenti superficiali.
Temperatura di fusione
Una proprietà chimico fisica con un grande impatto in termini di riduzione dei costi è il basso punto di fusione della Zamak che ne rende possibile la pressofusione in camera calda. A differenza dell’alluminio, che ha un punto di fusione molto più elevato e che è pressofuso in camera fredda, la zama consente un risparmio energetico dato dalla diversa tecnologia di fusione impiegata. Il vantaggio dato dalla pressofusione in camera calda è ulteriore ed è relativo al tempo: la pressofusione in camera calda è un processo più veloce della pressofusione in camera fredda e ciò consente di aumentare la produttività. Un altro elemento di risparmio, sempre correlato alla temperatura di fusione, è costituito dal fatto che lo stampo, sottoposto a minori temperature, incorre in una minore usura ed ha quindi una vita più lunga, con benefiche ripercussioni soprattutto nel caso della produzione di grandi volumi.
Economia circolare
In questo breve passaggio sulle qualità della zama rispetto ad altri metalli merita di essere ricordata un’ultima proprietà: la riciclabilità. Lo zinco infatti si inscrive nei processi di economia circolare e va quindi incontro alle recenti tendenze di sostenibilità ambientale. La riciclabilità dello zinco non si traduce solo in un vantaggio per il consumatore finale, che può riciclare i propri prodotti ed elettrodomestici, ma è anche un importante fattore di riduzione dei costi per il produttore di pressofusi. Lo zinco infatti, se gli accordi con il cliente lo consentono, può essere rifuso e, in percentuali controllate, reintrodotto nel processo produttivo, con evidenti conseguenze di riduzione dei materiali di scarto e di ottimizzazione dei processi produttivi.
Se desideri leggere di più sulla possibilità di riciclare la zama clicca qui se quello che cerchi è invece un approfondimento sull’economia circolare dello zinco ti consigliamo di leggere l’articolo Pressofusione ed economia circolare: il ruolo dello zinco.
Ottimizzazione del processo produttivo
Non sono solo le proprietà dello zinco come materiale ad essere importanti ai fini della riduzione dei costi nella pressofusione. Anche il processo produttivo con cui il metallo viene lavorato è molto importante. Infatti le tecniche di pressofusione e i macchinari, per essere efficienti, devono essere aggiornati allo sviluppo tecnologico: sono quindi necessarie ricerca e innovazione costanti.
Per un’overview generale su queste tematiche si consiglia di leggere Come migliorare il processo produttivo per l’industria della pressofusione.
Automazione e tempo ciclo
Un importante passo in direzione di riduzione dei costi è, ad esempio, l’introduzione di automazione nei processi produttivi. L’automazione rende infatti il sistema più efficiente diminuendo la percentuale di scarti e consentendo agli operatori a bordo macchina di dedicarsi ad attività a maggior valore aggiunto.
L’acquisizione di automazione è poi strettamente correlata alla capacità di aggiornare ed implementare il parco macchine. Grazie all’acquisto di nuove macchine, infatti, attività prima manuali diventano meccaniche facendo sì che lead time, tempo ciclo e percentuale di scarto diminuiscano a fronte di un aumento di produttività. Il tempo ciclo, in particolare, è molto importante in relazione alle strategie di riduzione dei costi, diminuire il tempo ciclo vuol dire infatti incrementare l’OEE, l’indice di rendimento produttivo dello stabilimento, e di conseguenza la produzione. Nel settore specifico della pressofusione in camera calda, inoltre, la diminuzione del tempo di ciclo rappresenta un’ulteriore opportunità di risparmio perché, in un tempo ciclo ridotto, aumenta la potenza termica che il materiale fuso apporta allo stampo con una diminuzione dei fronti freddi e dei difetti correlati.
Per approfondire gli apporti dell’automazione al processo produttivo leggi L’importanza dell’automazione per migliorare il processo produttivo; per scoprire di più sul tempo ciclo e sulla sua ottimizzazione si consiglia invece di leggere l’articolo Riduzione dei costi tramite l’ottimizzazione del tempo ciclo.
Simulazione
Un’ulteriore strategia per ottimizzare il processo produttivo è quella di ricorrere a software di simulazione che consentano di prevedere quanto avverrà durante il processo di pressofusione. La simulazione è un utile strumento per prevenire problemi, errori e difetti durante lo stampaggio dei pressofusi ed è, inoltre, un fondamentale ausilio in fase di progettazione, prototipazione e test.
Puoi trovare un approfondimento sui vantaggi apportati dalla simulazione nella pressofusione di zinco cliccando qui.
Certificazioni qualitative
Una garanzia dell’ottimizzazione del processo produttivo e della conseguente riduzione dei costi è l’ottenimento di certificazioni di qualità. Smeta 4 Pillars, ad esempio, è una certificazione di standard qualitativi, gestione ambientale, integrità aziendale, salute e sicurezza con importanti ripercussioni a livello di riduzione dei costi. Smeta 4 Pillars infatti, attraverso la condivisione di approcci standardizzati, migliora e uniforma il processo produttivo proteggendo la brand reputation e garantendo una filiera etica.
Co-design
Il co-design consiste in una serie di attività che hanno come obiettivo l’aumento del valore del prodotto e il suo miglioramento in termini di qualità ed efficienza. Spesso queste attività non si traducono in un aumento dei costi di produzione ma, al contrario, risultano in una diminuzione di prezzo. Già in fase di progettazione, infatti, attraverso il co-design, è possibile concordare con il cliente riduzioni di peso, eliminazione di lavorazioni secondarie, ottimizzazioni dello stampo e una serie di altre azioni che si traducono direttamente in una notevole riduzione dei costi. Ottenere un disegno già ottimizzato per la mass production permette così al cliente di avere un prodotto finale in linea con le attese e con meno rischi e scarti. Come ulteriore garanzia di riduzione dei costi in fase di co-design è possibile fare analisi di valore VA/VE ed ottimizzare il DFM. Le analisi di valore VA/VE sono un sistema di risoluzione dei problemi che permette di identificare efficacemente i costi superflui rendendone possibile una riduzione mentre il DEF, Design for Manufacturability, è uno studio di fattibilità in cui si valuta il design di un prodotto e in cui si propongono adattamenti, trattamenti particolari e modifiche strutturali che rendono possibile ottimizzarne la produzione.
Per una trattazione di più ampio respiro sul co-design si suggerisce di leggere l’articolo Design del prodotto per la pressofusione.
I metodi per realizzare riduzione dei costi nella pressofusione di zinco ed ottimizzare processi e prodotti non si esauriscono qui. Dalla lettura di questo articolo dovrebbero però essere emersi quelli che sono solo alcuni, ma evidenti, vantaggi.