Riduzione dei costi tramite l’ottimizzazione del tempo ciclo
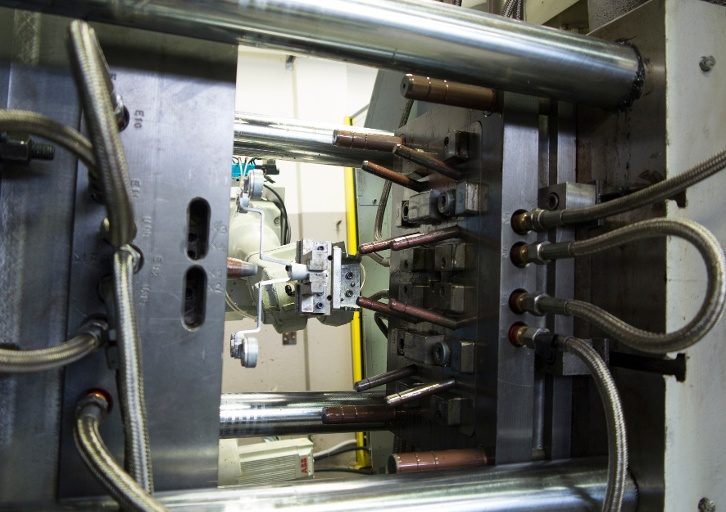
In questo post parleremo della struttura del tempo ciclo e di come la sua ottimizzazione possa portare numerosi vantaggi per l’azienda.
I cicli standard
Nella pressofusione si parla di tempo ciclo per indicare l’intervallo di tempo che intercorre tra l’inizio di un ciclo di iniezione e il successivo. Esso viene calcolato attraverso una sommatoria dei tempi parziali del processo di pressofusione. Un ciclo standard è composto infatti da diverse fasi:
- Tempi di iniezione:
Il pistone percorre un percorso ad una velocità di 1° fase, in cui il materiale viene portato fino all’ugello; viene successivamente accelerato dall’espansione dell’azoto nell’accumulatore per raggiungere la velocità di 2° fase, in cui la cavità viene riempita. - Tempi tecnici di stampaggio:
Comprendono le fasi di compattamento e raffreddamento materiale, coprendo quindi il passaggio del metallo dallo stato liquido a quello solido. Il compattamento avviene per compensare il ritiro volumetrico che viene generato dalla transizione di fase. - Tempi movimento stampo/lubrificazione:
Includono apertura e chiusura dello stampo, il movimento degli estrattori in avanzamento e ritorno e la lubrificazione dello stampo che può essere manuale, tramite cartesiano o ugelli fissi. - Tempi di controllo-opzionali:
Sono variabili in funzione del sistema di svincolamento pezzo utilizzato. In caso di prelievo da parte di un robot sarà infatti consigliabile un controllo della stampata tramite fotocellula, mentre in un sistema a caduta su bilancia sarà necessario tarare lo strumento con il peso previsto in modo da rilevare la presenza di pezzi nello stampo.
A valle del ciclo di stampaggio, sono necessarie operazioni di smaterozzatura e, per prodotti critici, di rifinitura. Alcune di queste operazioni possono essere eseguite manualmente da un operatore sulla postazione, mentre altre, come ad esempio la filettatura, richiedono l’invio del grezzo ad aziende esterne.
Alternativamente è possibile integrare la produzione con un sistema di automazione a bordo macchina. Tramite macchinari automatizzati che si occupano di rimuovere la materozza è possibile effettuare saving sulle ore uomo, che potranno essere spese per esempio in attività Kaizen.
Un ulteriore efficientamento è possibile tramite l’automatizzazione e l’integrazione a bordo pressa di lavorazioni di precisione come la filettatura, che riducono i tempi di transito del WIP all’interno dello stabilimento. Grazie all’impiego di macchinari integrati allo stampaggio in grado di svolgere lavorazioni complesse è possibile ridurre i lead time ed andare incontro alle esigenze del cliente in modo più agile.
Il tempo necessario a svolgere l’intero ciclo dell’automazione va quindi ad unirsi o sovrapporsi al tempo ciclo di stampaggio, componendo il tempo ciclo standard del codice prodotto.
Misurare le performance aziendali
Per quantificare il rendimento di un’industria, è possibile fare riferimento a 2 indici:
– il primo è l’OEE (Overall Equipment Effectiveness), un indice percentuale ricavato dal prodotto di disponibilità, efficienza e qualità. L’indice fa riferimento al rendimento produttivo dello stabilimento;
– il secondo è l’OTIF (On time in full) che quantifica in punti percentuali le capacità logistiche dell’azienda di inviare la quantità richiesta di prodotti entro i tempi accordati.
L’ottimizzazione dei tempi di ciclo incrementa l’indice OEE aumentando l’indice di efficienza. Inoltre, grazie alla riduzione dei tempi produttivi, aumentano le ore macchina libere, consentendo all’azienda di evadere un maggior numero di ordini senza variare le ore di apertura impianto.
Come visto precedentemente, l’indice OEE si compone di 3 fattori:
- La disponibilità, ovvero il rapporto tra ore macchina lavorate e ore macchina disponibili;
- L’efficienza, ovvero il rapporto tra pezzi prodotti e pezzi producibili;
- La qualità, ovvero il rapporto tra pezzi conformi e pezzi prodotti.
Spesso il miglioramento dei tempi di ciclo nella pressofusione ha un impatto anche sulla qualità dei getti. Una riduzione dei tempi comporta un maggior numero di iniezioni/ora, incrementando la potenza termica che il materiale fuso apporta allo stampo. In questo modo incrementa a sua volta la qualità superficiale del getto, poiché diminuisce il numero di fronti freddi che generano frastagliature sulla superficie.
I vantaggi offerti da azione di ottimizzazione sono quindi molteplici e in grado di migliorare l’intera produzione. Vediamo ora più nel dettaglio alcune strategie per il miglioramento del ciclo produttivo.
Come effettuare un’ottimizzazione del tempo ciclo su stampi con automazione
Il primo passo è definire se intervenire sui tempi di stampaggio o sui tempi di automazione. In un ciclo produttivo ideale i due tempi coincidono, cioè i processi sono parallelizzati e non vi sono colli di bottiglia.
Per definire la priorità di intervento si può utilizzare il cosiddetto diagramma di Pareto dei tempi parziali: il diagramma di Pareto è composto da un istogramma della distribuzione percentuale di un fenomeno, ordinato in senso decrescente e permette di identificare visivamente i fattori principali. Dopo lo studio del grafico sarà possibile individuare i punti da ottimizzare: prediligeremo infatti i fattori ad impatto maggiore.
Una volta redatto il grafico, si effettua una separazione tra tempi indipendenti e tempi mascherati.
Con tempi indipendenti si indicano azioni concatenate, che avvengono in sequenza l’una con l’altra. La riduzione di un tempo indipendente comporta ad una riduzione immediata del tempo ciclo.
I tempi mascherati invece definiscono azioni che avvengono in parallelo ad altre azioni; la riduzione di un tempo mascherato senza la riduzione del suo parallelo non porta a variazioni sul tempo ciclo.
Intervenire sui tempi indipendenti: esempio automazione con prelievo tramite robot
Una volta definito di ridurre i tempi dell’automazione, si procede filmando l’intero ciclo del robot, cioè dal prelievo in macchina al deposito. Grazie a queste riprese, sarà possibile stilare un elenco accurato dei movimenti e delle operazioni effettuate con la loro durata. Partendo da questi dati si potrà decidere se intervenire ottimizzando la velocità dei movimenti o modificandone la traiettoria.
I movimenti che un robot di prelievo stampata effettua in un ciclo di lavoro sono: allineamento alle colonne, entrata nell’ingombro pressa, prelievo della stampata, uscita da ingombro pressa, passaggio al punto di controllo e deposito.
Prima di procedere all’ottimizzazione effettiva, vengono effettuate simulazioni che permettono di formulare delle ipotesi di tempo ciclo, per poi decidere come intervenire: talvolta è sufficiente modificare la velocità di movimento, altre volte sarà invece necessario eliminare movimenti superflui.
Intervenire sullo stampaggio
Lavorare all’ottimizzazione dei sistemi di stampaggio presenta sfide maggiori, poiché la maggior parte delle operazioni prevede tempi pressoché fissi, come la compressione del pistone ed il raffreddamento del getto. Alcune possibili migliorie sono:
- Il tempo di raffreddamento può essere ridotto modificando la termoregolazione dello stampo tramite l’ausilio di centraline ad olio/acqua; la riduzione di tempo di permanenza del getto nello stampo può quindi essere compensato da una riduzione di T° del fluido termoregolatore.
- La durata dello stampaggio. La funzione di prefilling fornisce un utile supporto in questo senso, in quanto il saving sul ciclo è assimilabile alla durata della 1° fase del pistone di iniezione. Lo spostamento del pistone in 1° fase viene commutato da tempo indipendente a tempo mascherato alla chiusura stampo.
È invece possibile intervenire in modo più sensibile sui tempi di estrazione (ritardo partenza, velocità avanzamento, velocità ritorno, ritardo ritorno, numero corse), apertura/chiusura stampo (velocità apertura/chiusura, corsa apertura) ed intervento lubrificazione (ritardo partenza, durata lubrificazione).
Se si lavora con un sistema automatizzato bisogna tenere conto della necessità di sincronizzare i movimenti del robot con le nuove tempistiche. L’ottimizzazione dei tempi ciclo può essere molto variabile e portare a riduzioni superiori al 20-30%, consentendo quindi un buon risparmio in termini economici per l’azienda.