Design del prodotto per la pressofusione
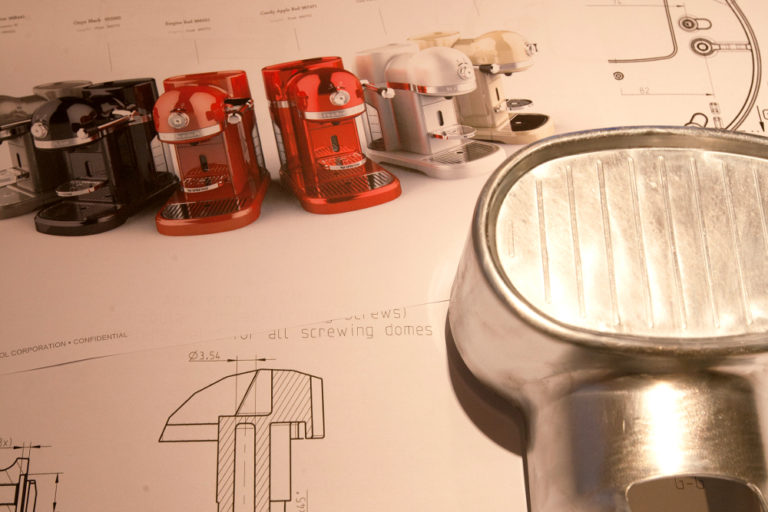
Il termine design del prodotto definisce il processo di progettazione di un prodotto caratterizzato da specifiche caratteristiche estetiche e funzionali, che deve essere conforme al processo di produzione in serie. Il design del prodotto è dunque un processo che necessita di essere sviluppato considerando i diversi aspetti che caratterizzano un componente e, di conseguenza, se realizzato con la tecnologia della pressofusione, richiede l’integrazione di diverse attività, quali servizio di co-design, compilazione di un DFM, progettazione dello stampo, simulazione e analisi delle lavorazioni successive.
Il design del prodotto è un’attività strettamente correlata alla progettazione del processo produttivo: i due concetti si influenzano a vicenda, infatti il prodotto deve essere conforme alla produzione di massa e il processo produttivo deve al contempo tenere in considerazione le specificità del prodotto. Il design del prodotto è un processo complesso e sfaccettato, che non concerne solamente prodotto e produzione, ma anche scelta dei materiali, caratteristiche estetiche e funzionali, lavorazioni meccaniche, trattamenti superficiali e qualità richiesta dal cliente.
Servizio di co-design
Allo scopo di ottenere un risultato equilibrato in termini di estetica, funzionalità e fattibilità, il design del prodotto è spesso sviluppato da un’azienda manifatturiera insieme al cliente che ha ordinato il prodotto. La cooperazione tra fornitore e cliente viene definita servizio di co-design: una collaborazione che promuove la condivisione di informazioni e know-how, al fine di conseguire risultati soddisfacenti per entrambe le parti. Gli ingegneri e i tecnici procedono all’analisi delle caratteristiche fisiche e meccaniche del prodotto, così da trovare soluzioni per assicurare la funzionalità e la fattibilità produttiva, ottenendo di conseguenza un riscontro positivo da parte dei clienti.
Il servizio di co-design apporta benefici non solo in termini di ottimizzazione di processo e design, ma anche relativamente alla relazione tra cliente e fornitore: un continuo scambio di informazioni promuove incremento di fiducia e stima reciproca e permette, inoltre, di accrescere le conoscenze di entrambe le parti.
Per ulteriori informazioni relative al servizio di co-design, clicca sul post sotto:
• Vantaggi del co-design: alleggerimento mirato
DFM: studio di fattibilità del prodotto
Cliente e fornitore si scambiano informazioni relative al design del prodotto e al suo processo produttivo attraverso un documento denominato DFM: Design For Manufacturability, cioè uno studio di fattibilità del prodotto. Lo scopo di un DFM è, infatti, quello di presentare il prodotto in relazione al suo processo produttivo, per analizzare la fattibilità tecnica del progetto e suggerire soluzioni al fine di facilitare la produzione. Attraverso questo documento i tecnici possono stabilire se il design è conforme ai sistemi tecnologici del dipartimento di produzione e, successivamente, possono apportare modifiche a determinate caratteristiche del prodotto o delle fasi di produzione.
La scelta della pressofusione come metodo di produzione implica l’attuazione di specifiche analisi inerenti ad angoli di sformo, estrattori e punti di iniezione: il design del prodotto è, infatti, strettamente collegato alla progettazione dello stampo, e di conseguenza al processo produttivo. L’utilizzo di stampi risulta vantaggioso poiché consente la replicabilità del componente, ma allo stesso tempo richiede specifiche analisi tecniche che permettano di ottenere uno stampo adatto per il prodotto: il DFM contiene tutte le informazioni necessarie al raggiungimento di questo obiettivo.
Per conoscere nel dettaglio la struttura di un DFM, ecco un post sull’argomento:
• Design del prodotto per pressofusione: ottimizzare il DFM
Progettazione dello stampo
Considerando la pressofusione come metodo di produzione, il primo aspetto da esaminare è la progettazione dello stampo: l’elemento centrale del processo di pressofusione. Cliente e fornitore collaborano per sviluppare un sistema che sia adeguato sia per il componente che per lo stampo, considerando le caratteristiche estetiche e funzionali del prodotto, ma anche le proprietà meccaniche dello stampo: deve essere resistente, solido e funzionale al processo di produzione.
Innanzitutto è necessario verificare la producibilità del prodotto con il metodo della pressofusione, analizzando le dimensioni e la geometria del componente. Una volta che la geometria e le caratteristiche tecniche sono state definite, il processo di progettazione dello stampo può iniziare: questa fase prevede l’analisi delle specifiche tecniche del prodotto, del numero di cavità, dell’area di proiezione, del volume e della forma dello stampo. I due elementi principali che costituiscono la progettazione dello stampo sono il design del sistema di alimentazione a camera calda e la simulazione: la modalità di alimentazione rappresenta infatti l’elemento centrale della progettazione dello stampo, mentre la simulazione costituisce un utile strumento per definire i parametri più appropriati da applicare prima che il componente venga prodotto.
Progettazione del sistema di alimentazione a camera calda
Nella realizzazione dello stampo un elemento centrale da considerare è la progettazione del sistema di alimentazione a camera calda. Infatti, il metodo di alimentazione influenza l’ottimizzazione della produzione e le caratteristiche del prodotto. Il diffusore e il canale di colata sono i due elementi principali che compongono il sistema di alimentazione: la definizione della loro configurazione e dimensione risulta fondamentale per l’output finale del processo di pressofusione, poiché la scelta di diverse forme conduce a diversi risultati e può inoltre determinare una riduzione di potenziali difetti sul pressofuso.
Per informazioni dettagliate sul sistema di alimentazione a camera calda, di seguito un post sull’argomento:
• Ottimizzazione del processo di pressofusione: sistema di alimentazione
Simulazione
Come precedentemente menzionato, la simulazione costituisce un valido strumento per il design del prodotto e dello stampo: con software di simulazione, come programmi CAD e software 3D, gli ingegneri esaminano le proprietà tecniche del prodotto e definiscono i migliori parametri da applicare. Questi dispositivi rappresentano un supporto fondamentale per l’analisi di caratteristiche fisiche, dal punto di vista strutturale e della resistenza, e consentono agli ingegneri di identificare preventivamente potenziali criticità sul pressofuso, riducendo così eventuali problemi che potrebbero emergere a posteriori. Infatti, già nelle prime fasi del riempimento dello stampo potrebbero verificarsi errori che comprometterebbero la produzione del pezzo, ad esempio una solidificazione del metallo troppo rapida: la simulazione aiuta a evitare queste problematiche fin dal principio.
Per ulteriori informazioni sulla simulazione, ecco una serie di case studies:
• Simulazione per pressofusione: conservazione dello stampo e ottimizzazione dei parametri
• Simulazione per pressofusione: studio della porosità da ritiro
• Simulazione per pressofusione: studio per la riduzione degli scarti
• I vantaggi della simulazione HPDC nella pressofusione
Lavorazioni successive allo stampaggio
Il design del prodotto riguarda anche l’analisi di lavorazioni successive che devono essere effettuate a seguito della fase di stampaggio. Infatti, durante la progettazione di un prodotto è importante considerare eventuali lavorazioni successive a cui il pezzo dovrà sottoporsi: le operazioni successive allo stampaggio possono essere lavorazioni meccaniche, trattamenti superficiali, operazioni di assemblaggio o processi di automazione. Prestare attenzione a queste lavorazioni già nella fase di design del prodotto consente di effettuare specifiche azioni e impostare determinati parametri al fine di ottenere un risultato senza difetti. Di seguito alcuni esempi di lavorazioni successive.
Lavorazioni meccaniche
Tra le più diffuse lavorazioni meccaniche figurano filettatura e alesatura: se un componente necessita di essere filettato, già nella fase di progettazione dello stampo dovranno essere definiti specifici parametri per agevolare quest’operazione.
Trattamenti superficiali
Se un prodotto è soggetto a trattamenti superficiali, come verniciatura o cromatura, è importante prevedere in anticipo potenziali difetti che potrebbero manifestarsi dopo il trattamento. Ad esempio, alcuni trattamenti superficiali vengono effettuati a temperature molto alte che possono potenzialmente determinare la formazione di inclusioni d’aria nel componente: durante la fase di design dello stampo sarà quindi necessario prevedere l’evacuazione d’aria.
Assemblaggio
Relativamente all’assemblaggio, è opportuno definire specifiche tolleranze che siano funzionali a questa lavorazione. Per esempio, se il pezzo deve essere inserito in un altro componente, come un perno e un foro, è necessario prevedere la giusta interferenza tra i due.
Automazione
L’automazione rappresenta un fattore comune a tutte le lavorazioni successive: le operazioni automatiche per i trattamenti successivi allo stampaggio garantiscono un’adeguata produttività e costi ridotti.
Vantaggi design del prodotto
Il design del prodotto è una fase indispensabile nella produzione di un componente poiché consente di identificare i processi e le caratteristiche maggiormente performanti, allo scopo di produrre eccellenti risultati in termini di estetica, funzionalità e conformità al processo di produzione. Sviluppare un processo di design del prodotto ben strutturato è perciò fondamentale per ottenere importanti benefici, quali riduzione dei costi di produzione, soddisfazione del cliente e produzione di componenti esteticamente accattivanti, funzionali e conformi alla produzione di massa.