Resistenza meccanica: verifica del carico di rottura per i componenti in zama
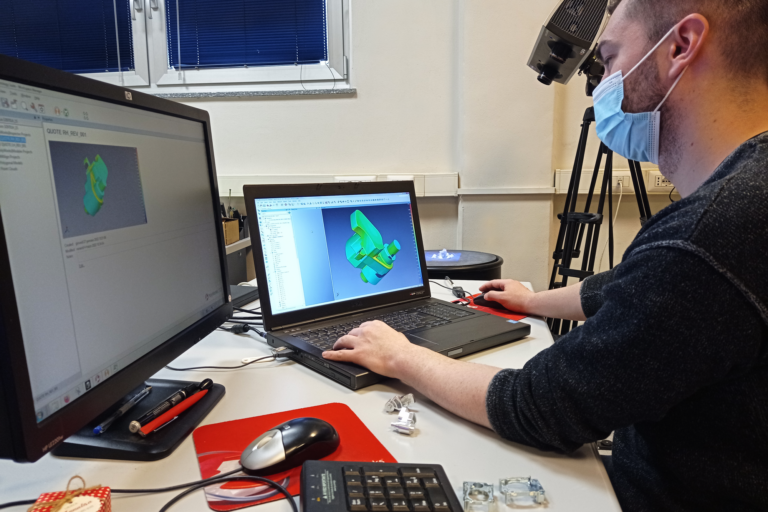
In termini di resistenza meccanica il carico di rottura più comunemente definito nel mondo tecnico con l’inglese ultimate tensile stress (UTS), è il limite massimo di forza esterna applicata oltre al quale un materiale perde le sue specifiche funzionali in termini di resistenza. Le prove di verifica del carico di rottura, che variano a seconda del tipo di sollecitazione a cui è sottoposto il materiale e che saranno descritte in seguito nel nostro caso sono test da effettuare su un componente in fase di produzione.
In tema di resistenza meccanica e più in dettaglio di carico di rottura in questo post sarà brevemente definita la funzione dei test di rottura nel controllo della qualità strutturale di pressofusi in zama nel corso della produzione. Sarà inoltre descritto lo strumento utilizzato per l’esecuzione di queste prove atte a garantire il rispetto delle specifiche del componente. Di seguito verrà descritta qualche case study relativa all’argomento principale.
Carico di rottura: prova di resistenza a rottura di un pezzo o di un assieme
Come anticipato il carico di rottura è la forza che è necessario applicare ad un pezzo per provocare snervamento e/o rottura e si misura in mega-pascal, indicato con il simbolo MPa, che è la principale unità di misura della pressione, cioè della forza sull’unità di superfice.
Per procedere con questo test si applica la forza in un punto del pezzo, prestabilito e concordato con il cliente, allo scopo di osservare il carico necessario per provocare la sua rottura o il suo snervamento. In questo modo si può testare la quantità di forza necessaria affinché il pezzo posto in esame perda le specifiche proprietà meccaniche, ovvero la capacità del componente di resistere ai carichi esterni e sia, di conseguenza, inutilizzabile.
Per effettuare questo processo è necessaria una macchina specifica per prove di trazione/compressione da laboratorio.
Questa macchina è quindi estremamente importante perché le prove di resistenza a rottura sono tra gli elementi chiave per la verifica funzionale di un prodotto finito. Spesso infatti singoli componenti pressofusi in zama vengono montati in un ambiente o in un assieme che subisce varie sollecitazioni dall’esterno e queste forze, se non opportunamente considerate ed analizzate, potrebbero compromettere uno o più elementi del sistema mettendo a rischio la funzione del prodotto stesso. Un esempio molto chiaro di questo concetto è certamente il gruppo sterzo di un’automobile che subisce sollecitazioni differenti a seguito di diversi conducenti. I singoli elementi ed il sistema devono necessariamente essere in grado di svolgere la propria funzione senza rompersi anche in caso di forze eccessive applicate da conducenti con stili di guida estremi. Perciò il fatto di evitare la compromissione della funzionalità e quello di garantire la corretta resistenza meccanica dei componenti dello sterzo, costituiscono un fattore di sicurezza essenziale per la persona al volante.
Il carico di rottura: prove reali e simulazioni al computer (FEM)
Questo genere di test può anche essere simulato all’interno degli applicativi CAD (FEM) ma come è noto il processo di pressofusione, anche utilizzando la tecnologia del vuoto, non permette lo stampaggio di pezzi a densità teorica del materiale poiché a seguito del ritiro volumetrico durante il raffreddamento all’interno delle zone del pressofuso a massa maggiore si creano micro cavità, chiamate tipicamente “cavità da ritiro”, che potrebbero compromettere le prestazioni del prodotto in termini di resistenza meccanica. Queste variazioni di densità non sono completamente intercettate dai sistemi software di simulazione i quali possono risultare molto utili in fase di progettazione ma che, in termini di produzione, potrebbero mettere in discussione il raggiungimento delle specifiche richieste a causa dei risultati imprecisi rilevati dal programma di simulazione. Per questa ragione è consigliato utilizzare i programmi di simulazione per definire un’idea di realtà, una linea guida per la produzione e poi, direttamente in fonderia, procedere invece con controlli a campione durante lo stampaggio e verificare nel dettaglio ogni singolo aspetto legato alla resistenza meccanica.
Avere un costante controllo in tempo reale sulla produzione, verificando ciclicamente a campione, è quindi fondamentale per verificare se la produzione è conforme alle specifiche del cliente. Il vantaggio di utilizzare questi strumenti di controllo direttamente in produzione comporta quindi un controllo continuo e la capacità in tempo reale di agire per evitare eventuali interruzioni di linea.
In conclusione
Come abbiamo brevemente osservato precedentemente le prove in produzione del carico di rottura non sostituiscono le simulazioni, ma le affiancano con diversi obiettivi. Si tratta di prove importanti, periodiche durante la produzione, per garantire un processo affidabile e conforme alle specifiche.