I vantaggi della simulazione HPDC nella pressofusione
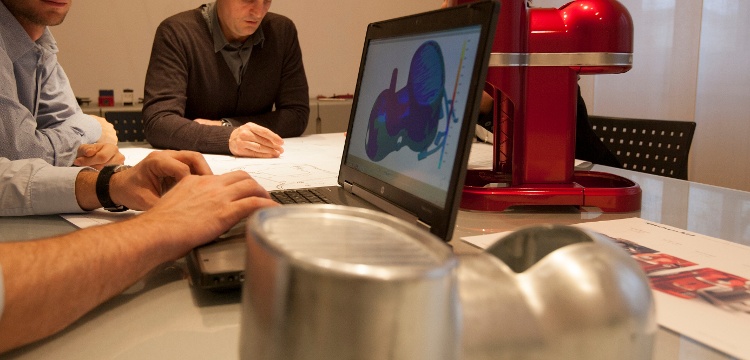
In questo articolo vedremo i vantaggi comportati dall’uso di un software di simulazione HPDC (High Pressure Die Casting) nella produzione dei pressofusi.
Si tratta di un argomento molto discusso tra gli specialisti di settore: già nelle prime fasi del riempimento dello stampo, infatti, si possono verificare errori che possono compromettere la riuscita del pezzo, legati magari ad una troppo rapida solidificazione del metallo. Tutto questo può essere previsto ed evitato grazie alla simulazione CFD.
Le complessità del processo di fusione
Quando si considera il processo fusorio del metallo si parla di una simulazione termo-fluidodinamica bifase, poiché il processo di lavorazione del metallo si compone di fenomeni di tipo cinetico e dinamico, scambi termici e passaggio di fase da liquido a solido. Inoltre, lo scambio termico è sia di tipo convettivo, dipendente cioè dai movimenti del flusso, che di tipo diffusivo, dato dalla differenza di temperatura del fluido e dello stampo.
Date queste problematiche la migliore soluzione è un software di simulazione.
Soprattutto nel caso della simulazione HPDC (pressofusione ad alta pressione) la complessità degli stampi e i parametri macchina aumentano il numero di variabili da considerare durante la simulazione. Inoltre, il processo produttivo è continuo e basato su cicli rapidi di riempimento ad alta pressione e raffreddamento. Queste caratteristiche, unite alle forme intricate e alla sottigliezza delle parti prodotte, aumentano notevolmente la complessità numerica della simulazione.
Con queste premesse risulta subito evidente come anche il processo di simulazione non possa essere semplice: le equazioni utilizzate nel processo sono risolvibili con un approccio analitico solo in casi molto semplici e limitati. Per questa ragione è necessario applicare un metodo di tipo numerico che implica un uso dispendioso delle risorse computazionali. L’approccio numerico prevede una semplificazione delle equazioni e una gestione del dominio – ovvero lo spazio finito in cui si trova l’elemento di studio – di tipo discreto.
Il dominio viene trasformato in quello che si definisce mesh, vale a dire una griglia di calcolo composta da celle di varie dimensioni. Per ognuna di queste celle vengono scritte le rispettive equazioni di equilibrio che comporranno il sistema globale e saranno risolte dal simulatore. Maggiore sarà il numero delle celle e minore la loro dimensione, maggiormente precisa sarà la simulazione.
Anche l’uso di determinati software gioca un ruolo fondamentale per ottenere i migliori risultati possibili: programmi come MagmaSoft, un software di simulazione CFD dedicato alla fonderia, utilizzano uno schema numerico di tipo LES (Large Eddy Simulation) che permette di calcolare senza approssimazione la turbolenza fino a vortici di medie e grandi dimensioni, permettendo così di ricostruire velocemente e con precisione il fenomeno studiato.
L’importanza degli studi preliminari per pressofusione
Chi studia il processo di pressocolata tramite strumenti di simulazione non può prescindere dal confronto con la realtà. Solo l’osservanza del processo reale permette di identificare le difettosità del fenomeno che possono quindi essere catalogate, diventando studiabili, riproducibili e quindi anche evitabili. Lo studio approfondito ed empirico del fenomeno reale è, inoltre, fondamentale per poter stabilire i valori delle condizioni al contorno. La loro individuazione, oltre che essere necessaria alla chiusura del sistema numerico, stabilisce l’aderenza del modello simulato con la realtà.
I difetti studiabili e prevenibili attraverso l’uso di una simulazione includono:
- Porosità;
- Giunzioni fredde (Temperature troppo basse durante il riempimento);
- Presenza di aria nel pressofuso;
- Inclusioni metalliche date dalla presenza di corpi estranei nel materiale fuso;
- Problemi di cavitazione o di erosione dello stampo;
Ognuna di queste possibili problematiche è legata a campi fisici del sistema individuabili in simulazione, quali velocità, pressione e temperatura: la porosità ad esempio è causata dalla distribuzione del materiale nello stampo ed è legata quindi alla velocità di immissione, alla pressione dell’aria nello stampo e alla distribuzione della temperatura durante la solidificazione. Attraverso l’uso di una simulazione HPDC è quindi possibile prevedere la formazione di sacche di vuoto che intaccherebbero la solidità e l’estetica del prodotto.
Un altro caso in cui la simulazione si rivela particolarmente efficace è nel prevedere i possibili danni causati allo stampo dalla cavitazione: si rischia infatti che lo stampo subisca un’erosione maggiore in presenza di variazioni di pressione. Per questo è necessario studiare approfonditamente la geometria del corpo, disegnando canali con forme e posizioni strategiche.
Simulazione HPDC: confronto con la realtà
Lo specialista dovrà quindi cercare le cause delle anomalie nei campi fisici del fluido, valutando caso per caso e affiancando ai dati matematici forniti dalla simulazione il valore aggiunto della sua esperienza pratica. Confrontare le aspettative date dalla simulazione con i risultati effettivi offre due vantaggi principali:
- da un lato, permette di aumentare la comprensione del fenomeno fisico che genera difettosità e di avvicinare chi lo studia a una risoluzione caso per caso, poiché difficilmente il percorso risolutivo sarà univoco;
- aumentare la capacità interpretativa dei risultati numerici per meglio capire quali campi o combinazioni di campi permettono di individuare i valori critici per lo sviluppo della difettosità;
Maggiore sarà l’esperienza accumulata dal tecnico specialista, migliori saranno quindi i risultati.