Simulazione per pressofusione: studio della porosità da ritiro
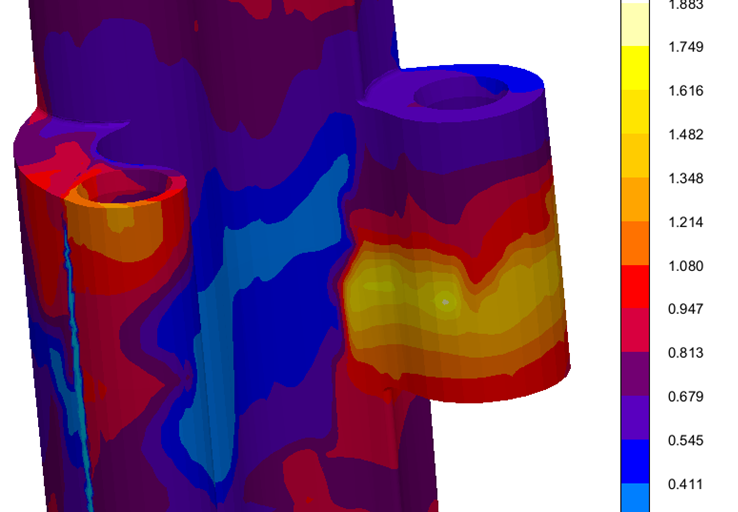
In questo post parleremo di uno studio reale dedicato al miglioramento delle caratteristiche meccaniche attraverso la riduzione della porosità da ritiro in un componente per il settore delle costruzioni. Questo post fa parte di una serie in cui spieghiamo l’importanza della simulazione per pressofusione presentando dei casi reali.
Caratteristiche meccaniche: uno studio nel settore costruzioni
Il prodotto che studieremo nel post di oggi è una cerniera per porte. Questo componente meccanico era progettato per essere sottoposto a sforzi di bassa-media intensità. A differenza di altri prodotti nel settore delle costruzioni, in questo progetto le caratteristiche estetiche non erano molto rilevanti, mentre le caratteristiche meccaniche e la resistenza all’usura erano fondamentali.
Obiettivo e fasi della simulazione
L’obiettivo della simulazione era di minimizzare i difetti che possono influenzare le caratteristiche meccaniche della cerniera della porta: la porosità e i fori. I requisiti per questo componente erano:
- assenza di cavità interne e bolle, causate da intrappolamenti di aria;
- riempimento corretto;
- nessun dettaglio mancante;
- bassa porosità da ritiro sia internamente che in prossimità del canale di alimentazione;
Grazie all’esperienza precedente nella produzione di pezzi simili, i nostri tecnici sapevano che la porosità è uno degli aspetti più critici per le cerniere delle porte: la presenza di buchi e cavità, causate dal ritiro del componente in prossimità del canale di alimentazione, potrebbe ridurre la resistenza e persino causare la rottura del componente sotto sforzo. Inoltre, un raffreddamento scorretto delle parti potrebbe causare picchi di calore sulla superficie dello stampo, portando alla formazione di cavità sulla superficie del componente.
L’analisi di simulazione si è concentrata quindi sulla fase di solidificazione, con l’obiettivo di trovare una configurazione che permetta un raffreddamento omogeneo delle parti, evitando così la formazione di aree più calde e prevenendo la porosità.
Risultati
Lo studio delle fasi di riempimento si è concentrato sull’analisi della distribuzione degli intrappolamenti di aria. Come si può vedere dall’immagine seguente, la quantità di aria è minima ed è equamente distribuita in piccole dosi attraverso l’intero componente.
La porosità è stata analizzata osservando il comportamento del pezzo durante la fase di solidificazione: il punto più critico è il canale di alimentazione, dove la lega solidifica e si contrae durante la fase di raffreddamento.
A differenza di altre parti simili prodotte in precedenza, per questa simulazione si è deciso di orientare il condotto di alimentazione parallelamente agli assi dei fori, e non perpendicolarmente. Inoltre, la sua configurazione geometrica è ottimizzata per evitare la creazione di punti caldi sulla superficie delle parti.
Come si può vedere dall’immagine, nella nuova configurazione la superficie vicina al canale di alimentazione solidifica molto più rapidamente, diminuendo di conseguenza il rischio di porosità da ritiro.
L’area di congiunzione solidifica rapidamente (colorata in azzurro), contemporaneamente al resto della superficie del prodotto, riducendo il rischio di porosità superficiale. L’area più critica è quella subito sotto alla giunzione – cerchiata in rosso – dove il raffreddamento è molto più lento a causa della vicinanza del canale di alimentazione.
Ma come si può vedere dall’immagine indicata come “50% liquido” la criticità dovrebbe essere ormai risolta: l’area cerchiata è solida (colorata in azzurro) mentre il centro del componente è ancora liquido (in giallo).
L’immagine qui sopra raffigura la simulazione dello stampo: il volume vicino all’attacco di colata porta ad una solidificazione davvero lenta e alla formazione di porosità da ritiro come conseguenza diretta. Invece, il ri-posizionamento della giunzione ha ridotto il problema della porosità grazie ad un raffreddamento più rapido del metallo fuso.
Il risultato della simulazione è stato confermato dopo l’utilizzo dello stampo: il problema della porosità da ritiro, tipica di questo tipo di prodotti, è stato completamente eliminato.
Riassumendo, l’esperienza ottenuta trattando con casi simili ha permesso a Bruschi di identificare le criticità già dalla fase di design dello stampo e di studiare una soluzione attraverso l’uso della simulazione. L’obiettivo era di migliorare la resistenza del componente riducendo la porosità da ritiro: questo rende il componente più resistente all’usura e evita le rotture sotto sforzo. Lo studio di simulazione della fase di solidificazione ha confermato che posizionare il condotto di alimentazione parallelo agli assi dei fori aumenta la velocità di raffreddamento, riducendo così il rischio di porosità.
Ancora una volta, la buona riuscita di questo studio dimostra l’importanza della simulazione nella pressofusione: l’uso di nuove tecnologie può aiutare ad ottenere differenze competitive sul mercato anche in un settore millenario come quello della lavorazione dei metalli.