Riduzione dei difetti di pressofusione attraverso il redesign dello stampo
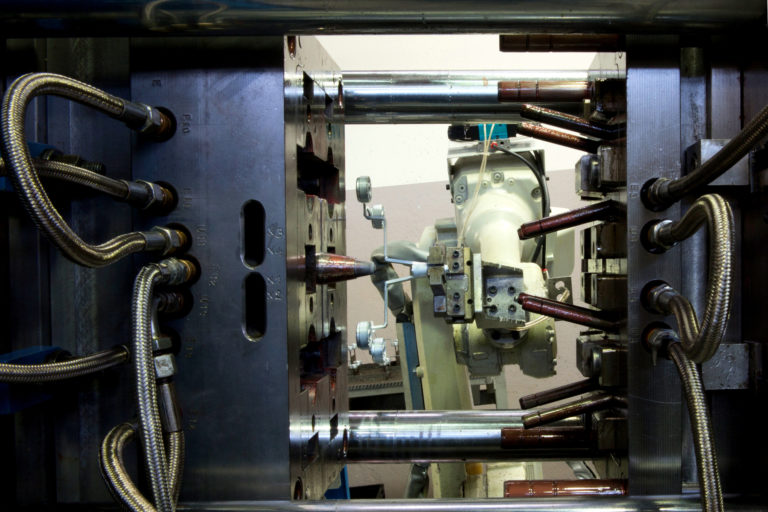
In questo articolo analizzeremo un case study relativo alla riduzione dei difetti di pressofusione ottenuta attraverso la riprogettazione dello stampo. Le modifiche apportate si sono rese necessarie a causa dello stato di usura dello stampo, realizzato 10 anni fa, e sono state definite a seguito di una fase di studio e analisi del precedente design dello stampo.
In linea con il principio della lesson learned, gli ingegneri Bruschi hanno analizzato le performance di produzione del pressofuso e definito nuovi parametri basandosi sulle conoscenze apprese negli anni al fine di ottenere un componente che soddisfasse gli standard qualitativi richiesti. Inoltre, è stato possibile apportare accurate modifiche grazie all’impiego di tecnologie avanzate, quali software di simulazione, che hanno permesso di progettare soluzioni al fine di ridurre i difetti di pressofusione.
Fattori che determinano la qualità superficiale di un pressofuso
La qualità superficiale di un componente prodotto con la tecnologia della pressofusione può infatti essere determinata da molteplici fattori, quali termoregolazione dello stampo e temperatura del materiale iniettato nella cavità, ma dipende principalmente dalla modalità di riempimento del canale di alimentazione. La progettazione di un canale adeguato, che consenta un riempimento simmetrico delle cavità dello stampo, costituisce quindi un requisito fondamentale per evitare la formazione di difetti di pressofusione sul componente. Un canale di alimentazione asimmetrico o non convergente può, invece, determinare intrappolamenti d’aria nel pressofuso, nonché aree caratterizzate da evidenti marezzature causate da un riempimento disomogeneo.
Case study
Il componente oggetto del seguente case study è un componente della cerniera di una porta. Dopo anni di produzione del pezzo, utilizzando il primo stampo, a seguito dell’usura dello stesso sono emersi difetti di pressofusione sulla superficie del componente, quali marezzature, mancati riempimenti e porosità d’aria. A seguito dell’analisi dei parametri e della geometria dello stampo, gli ingegneri Bruschi hanno allora identificato l’errata modalità di riempimento delle cavità come causa principale dei difetti. Per risolvere questo problema si è quindi deciso di progettare e realizzare un nuovo stampo. Al fine di ridurre i difetti di pressofusione sono perciò state apportate modifiche in fase di progettazione, effettuando un appropriato redesign dello stampo, più specificatamente del canale di alimentazione.
Fase 1 – Simulazione
La prima fase del progetto di riprogettazione dello stampo ha riguardato la simulazione di riempimento delle cavità con il software di simulazione termofluidodinamica Magmasoft, che ha permesso di prevedere con buona approssimazione il comportamento del fluido durante la fase di riempimento. Magmasoft consente infatti di analizzare diversi parametri, quali temperatura del metallo in tutte le fasi del riempimento, pressione dell’aria nella cavità, velocità del fluido e presenza di zone interessate da intrappolamenti d’aria. Per ulteriori informazioni sulla simulazione, clicca sui post qui sotto:
• Simulazione per pressofusione: conservazione dello stampo e ottimizzazione dei parametri
• Simulazione per pressofusione: studio della porosità da ritiro
• Simulazione per pressofusione: studio per la riduzione degli scarti
Dalla simulazione sono emerse tre principali problematiche:
• riempimento asimmetrico
• canale di alimentazione non convergente
• disomogeneità di temperatura del materiale
Per definire al meglio le azioni correttive da attuare è stato necessario analizzare la geometria del prodotto: il componente presenta infatti una sezione superiore massiccia e una sezione inferiore più sottile. La sagoma del prodotto ha richiesto, di conseguenza, una particolare attenzione durante la progettazione del canale di alimentazione, poiché per ottenere un riempimento simmetrico e omogeneo delle cavità è risultato necessario l’inserimento di elementi che agevolassero la dinamica del fluido di riempimento.
Fase 2 – Redesign sezione superiore
A seguito della simulazione il riempimento della sezione superiore è risultato asimmetrico, causando così intrappolamenti d’aria nel pressofuso, con conseguente formazione di bolle d’aria sulla superficie del componente. La causa dell’asimmetria del riempimento è stata attribuita alle diverse velocità con cui il fluido iniziava a riempire la cavità. Infatti, la zama entrava dal punto di iniezione con un’elevata energia cinetica e proseguiva il suo percorso seguendo la geometria delle cavità, che la portava a riempire maggiormente e più velocemente determinati volumi, raggiungendo invece solo in un secondo momento quelle sezioni che non si trovavano nel verso del flusso principale.
Il primo problema da risolvere ha dunque riguardato l’entrata asimmetrica della zama nel gate: al fine di simmetrizzare l’entrata del metallo nella cavità, è stato aggiunto uno smorzatore alla fine del canale principale. Con la nuova configurazione il flusso, prima di dividersi, riempie lo smorzatore perdendo energia cinetica e prosegue il suo percorso verso la cavità con una velocità più uniforme.
Il secondo problema, sempre relativo alla parte superiore del pressofuso, era invece inerente alla divergenza del canale di alimentazione in alcune sezioni, che determinava l’insorgenza di turbolenze. Di conseguenza l’attività di redesign è stata effettuata procedendo con la progettazione di un canale convergente, il quale ha contribuito a canalizzare maggiormente il materiale e ad agevolare il riempimento delle cavità riducendo il distacco di vena fluida.
Fase 3 – Redesign sezione inferiore
La sezione inferiore del componente è invece differente dalla parte superiore. Si tratta di una parte più sottile e che quindi, con lo stampo iniziale, veniva riempita da materiale avente basse temperature, determinando così la formazione di marezzature e mancanze di materiale.
Osservando la geometria del componente risultava infatti evidente la difficoltà di riempimento omogeneo di tutte le cavità e in particolar modo della cavità inferiore: precedentemente la zama riempiva in primo luogo l’intera sezione superiore del pressofuso, che è caratterizzata da una dimensione considerevole, per raggiungere solo in un secondo momento la sezione inferiore. Il materiale arrivava quindi a riempire la sezione inferiore a una temperatura troppo bassa, tale cioè da non garantire un adeguato livello di finitura superficiale.
Per la risoluzione di questa problematica si è ricorsi alla progettazione di un’alimentazione dedicata, attraverso l’inserimento di due canali ausiliari. I canali sono stati inseriti nella parte inferiore del pezzo al fine di ottenere un riempimento più omogeneo, mantenendo la temperatura del materiale più stabile in tutto il pressofuso. Anche i due canali ausiliari, così come il canale principale di alimentazione, sono stati progettati in modo da ottenere un flusso simmetrico: a tal fine sono stati introdotti due ulteriori smorzatori all’inizio dei due canali ausiliari.
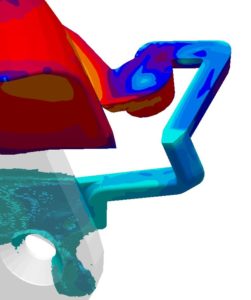
Inoltre, considerata la particolare geometria del prodotto, al fine di agevolare ulteriormente il riempimento in tutta la cavità, è stato progettato un profilo dell’attacco di colata parzialmente tangenziale in grado di indirizzare il materiale in zone critiche in termini di uniformità di riempimento. Le difficoltà che altrimenti si potrebbero incontrare, considerato che la sezione inferiore del pezzo presenta dei maschi che andranno a realizzare dei fori, i quali rendono il riempimento ulteriormente difficoltoso, sarebbero potenziali ostacoli al raggiungimento della qualità richiesta poiché costituiscono rallentamenti per il flusso della zama. Questo tipo di profilo, con attacco di colata parzialmente tangenziale, determina allora una migliore distribuzione della zama, facilitandone l’ingresso e il raggiungimento delle aree più critiche.
Risultati ottenuti
A seguito delle modifiche apportate gli ingegneri hanno eseguito la simulazione del riempimento delle cavità con il software Magmasoft e ne hanno avuto eccellenti risultati: le criticità precedentemente riscontrate hanno infatti registrato una notevole riduzione. Nello specifico, attraverso la riprogettazione del canale di alimentazione si è ottenuta una maggiore uniformità di riempimento, che di conseguenza ha determinato una riduzione dei difetti di pressofusione sulla superficie del prodotto.
Il presente case study conferma pertanto l’importanza del saper attingere dalle esperienze pregresse per la risoluzione di nuove problematiche, integrando know-how e tecnologia al fine di raggiungere risultati sempre più performanti. La riprogettazione dello stampo e l’utilizzo di Magmasoft hanno consentito di testare soluzioni diverse prima di procedere con l’effettivo stampaggio del prodotto, ottenendo così notevoli benefici in termini di qualità, tempistiche e costi.