Porosità da contrazione termica: cause e rimedi
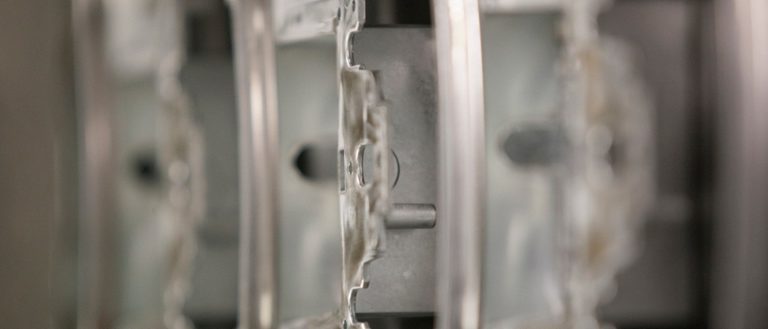
I difetti da porosità da contrazione termica si presentano come delle cavità all’interno dei componenti che possono causare fragilità nel materiale e, se poste sulla superficie, possono peggiorare le qualità estetiche e la resistenza alla corrosione.
Identificare la dimensione dei fori, la loro forma e superficie è cruciale per indicare quale difetto è presente e definirne le cause.
In ogni caso è importante distinguere la porosità da riduzione termica da quella ad intrappolamento d’aria: i buchi causati dalla presenza di aria hanno forme sferiche, mentre l’assenza di materia della porosità da restringimento presenta delle superfici angolari.
Ora analizzeremo in dettaglio i difetti da porosità da contrazione termica.
Cosa causa la porosità da contrazione termica?
La porosità da contrazione compare durante la fase di solidificazione del materiale, che comincia con la fase di riempimento dello stampo e termina quando ogni parte del materiale è completamente solidificata. La causa della formazione è la contrazione del materiale e, per questa ragione, la porosità è tanto intensa quanto elevato è l’indice di contrazione.
Il metallo iniettato negli stampi comincia la sua fase di raffreddamento quando entra in contatto con le pareti dello stampo. Lo scambio termico causa la solidificazione del metallo dalla superficie esterna al nucleo. Durante questa fase, il volume del metallo diminuisce causando un gradiente convettivo verso la superficie esterna. Per questa ragione le porosità si concentrano vicino le parti interne e massicce del componente.
Nella pressofusione dello zinco, in particolare per le leghe di zinco per fonderia, l’indice di contrazione del metallo è molto importante.
Altre caratteristiche della HPDC dello zinco che possono aumentare la porosità da contrazione sono l’alta conduttività termica dello zinco, aree di entrata per gli estrattori troppo piccole e un raffreddamento dello stampo ineguale.
Quando il design dello stampo e i parametri operativi non sono appropriati, le leghe di zinco potrebbero solidificare velocemente, il gradiente termico potrebbe essere molto elevato, si potrebbero formare aree calde e i canali sarebbero le prime parti del pressofuso a solidificare: in particolare quest’ultimo aspetto porta a diminuire l’effetto compressivo dei colpi. Tutto questo causa la porosità da contrazione termica.
Una volta analizzati questi punti, è importante lavorare su una componente geometrica che è fondamentale perché alcune geometrie possono presentare maggiori criticità di alter: ad esempio, un grande spessore delle pareti e una sezione trasversale troppo massiccia.
La porosità da contrazione in un prodotto nuovo o già esistente
Per un nuovo prodotto, al fine di evitare difetti è necessaria un’analisi in simulazione durante la fase di design. Se il componente esiste già, è necessario testare lo stampo ed analizzare i pressofusi colpiti dalla porosità di contrazione, in particolare le loro dimensioni e la posizione del difetto.
Come evitare i difetti con la simulazione di un nuovo prodotto
La porosità da contrazione può essere eliminata assicurando il flusso del metallo liquido ad alte pressioni durante la fase di raffreddamento. I tecnici dovrebbero utilizzare un software di simulazione per ottenere un analisi per la fase di raffreddamento del pressofuso.
Riguardo la porosità da contrazione è possibile identificare le forme e le posizioni della porosità e predire le sacche di aria attraverso una simulazione di fusione, tracciando i flussi.
Nel processo di pressofusione, grazie agli strumenti di simulazione, è possibile ottimizzare:
- La geometria dei pressofusi e degli stampi
- I parametri di fusione
- I sistemi di ingresso e raffreddamento
- La conformazione della matrice
I risultati dei dati sono necessari per indagare il problema e per diagnosticare il processo e prevenire i difetti.
Come risolvere la porosità da contrazione in un prodotto esistente?
A volte può succedere che un fornitore possa sostituire un altro fornitore per un pezzo particolare. Generalmente questo avviene per problemi di non-conformità dati da diverse ragioni: una di queste è la porosità da contrazione. In questo caso il nuovo fornitore dovrà lavorare direttamente sui prodotti, cercando di ottenere la soluzione migliore.
Ad esempio se le cavità hanno larghe dimensioni e sono sempre nella stessa posizione, vicino ai fori di immissione, potrebbe essere necessario intervenire su diversi fattori ed in particolare sugli estrattori e la geometria dei fori di entrata. Al contrario se le porosità hanno diverse frequenze e posizioni nel pressofuso, gli esperti dovranno lavorare sui macchinari e sui parametri operativi.
Per evitare la porosità da contrazione nei pezzi già esistenti, si può quindi lavorare in due modi:
- Modificare i parametri dei macchinari della pressofusione;
- Modificare lo stampo;
Qui sotto ci concentreremo su quali cambiamenti sono possibili.
Modificare i parametri dei macchinari per pressofusione
Prima di intervenire sui parametri delle macchine è importante controllarne la funzionalità. Infatti molto spesso i problemi di porosità possono essere causati da una manutenzione scorretta o assente.
Una volta che i fornitori hanno verificato la corretta funzionalità delle macchine, possono modificare i seguenti elementi:
- La pressione di lavoro: aumentare la pressione di lavoro ha sempre effetti positivi sulla porosità da riduzione, ma è importante non superare la forza bloccante della macchina. Per aumentare la pressione lavorativa è possibile diminuire il diametro dei colpi o aumentare la pressione idraulica;
- La temperatura di lavoro: modificando la temperatura e il tipo di fluido di raffreddamento è possibile raffreddare i punti caldi posizionati nelle zone di porosità;
Riassumendo, la pressione di lavoro e la temperatura sono i fattori macchina che contribuiscono a diminuire la porosità.
Modificare lo stampo
Cambiare la morfologia dello stampo significa evitare problemi quali la porosità da contrazione. Gli esperti possono lavorare su:
- Il canale di alimentazione: se le porosità sono vicine al foro di iniezione, il sistema più semplice ed efficace è quello di modificare l’estrattore in modo tale da rallentare la solidificazione nel canale di alimentazione e aumentare l’effetto comprimente dei colpi;
- Sistema di raffreddamento: come per le macchine, lo scopo è quello di raggiungere le zone di porosità al fine di raffreddate i punti caldi dello stampo;
Molti benefici derivano dall’uso di questi software di simulazione: ad esempio meno prodotti vengono scartati, il tempo di consegna è abbreviato e la qualità è migliorata. Queste previsioni portano ad una consistente riduzione dei costi, un miglioramento del materiale e una riduzione del consumo energetico e dalla quantità di scarti.