Design del prodotto per pressofusione: ottimizzare il DFM
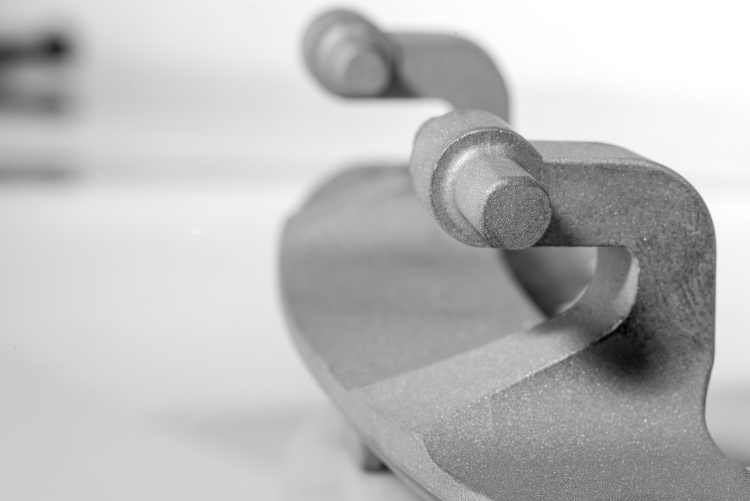
In questo articolo andremo ad analizzare il design del prodotto per pressofusione attraverso lo studio di un DFM (Design for Manufacturability) e suggerendo un sistema per ottimizzare e velocizzare il processo: il co-design.
Design del prodotto
Quando si parla di design del prodotto si pensa immediatamente alla componente estetica, ma essa è solo la parte visibile del complesso processo di design. L’aspetto è infatti inscindibile dalla funzione e dal sistema produttivo scelto, che determinano le regole a cui il designer dovrà sottostare. Il design evolve nel tempo e nella forma andando incontro quindi al gusto estetico dell’epoca, ma è anche vincolato da limiti imposti dal materiale scelto e dallo stato della tecnologia produttiva.
Il gusto estetico o la funzione dell’oggetto sono infatti intrinsecamente legati ai limiti imposti dal sistema produttivo e quindi, in quest’ottica, il metodo di lavorazione si rivela determinante.
La scelta di utilizzare come metodo produttivo la fusione in stampo impone di tenere conto di alcune esigenze, come gli angoli di sformatura, linee di chiusura e punti di estrazione. I vantaggi offerti dall’uso di stampi includono la riproducibilità del pezzo. Allo stesso tempo, a conseguenza di problemi nella fase di raffreddamento si potrebbe avere una riduzione di alcune caratteristiche meccaniche come la robustezza del pezzo, rendendo necessario intervenire tramite una diversa distribuzione del materiale o l’utilizzo di nervature strategiche.
Il processo di design del prodotto per pressofusione è quindi inscindibilmente legato al processo produttivo, rendendo necessario un rapporto tra cliente e fornitore che in questa fase si materializza con un DFM.
Struttura di un DFM
Un documento DFM funge da ponte comunicativo tra il cliente, i designer e i tecnici dell’azienda produttrice. Scopo di questo documento è presentare il prodotto in relazione con la sua produzione e riproducibilità nel tempo. Si tratta infatti di uno studio di fattibilità, ovvero il reparto tecnico dovrà valutare se il design si adatta alla tecnologie a disposizione dell’azienda e la disponibilità di un accordo economico.
Dopo l’analisi possono essere suggerite delle modifiche legate alla funzione produttiva o a migliorie strutturali per aumentare la resistenza del prodotto, senza però intaccare l’aspetto estetico o la funzionalità del prodotto richiesto. Queste richieste vengono incluse nel DMF, che si compone solitamente di questi punti:
- Aree critiche: la sezione in cui vengono evidenziati i punti che necessitano di trattamenti particolari o di modifiche strutturali;
- Area di Deformazione: a causa dell’uso dello stampo, è necessario tenere conto delle forze applicate nel momento dell’estrazione dallo stampo;
- Incongruenze o richiesta di precisazioni riguardo ai disegni;
- Tolleranze;
- Pianificazione delle posizioni degli estrattori;
La documentazione viene quindi trasmessa ai diversi uffici competenti al fine di trovare un accordo che soddisfi sia i requisiti tecnici che quelli estetico-funzionali.
L’utilizzo di uno stampo impone infatti una necessaria discriminazione tra le scelte estetiche e quelle strutturali, ma non sempre le prime dipendono dalle seconde. Ne sono un esempio i segni lasciati dal processo di estrazione, che si presentano come dei piccoli cerchi di uguali dimensioni e vengono solitamente posti sulla superficie interna o in altre posizioni non visibili. Lo stesso si può dire per i segni di iniezione, come l’attacco di colata.
Altre volte è invece l’aspetto tecnico a prevalere, come nel caso degli angoli di sformatura che non possono risultare inferiori a 1°, imponendo quindi cambiamenti al modello o il ricorso ad altri tipi di lavorazione. Un altro esempio sono le nervature di rinforzo, utilizzate per incrementare la resistenza del pezzo a stampa e ridurre il rischio di avvallamenti strutturali, che avrebbero ripercussioni sul piano estetico, ad esempio nelle strutture a cuspide.
O ancora, è possibile alterare il design originale per migliorare la funzionalità del prodotto, ad esempio creando concavità per ridurre o ottimizzare il bilanciamento del peso. La riduzione della massa può portare non solo ad un alleggerimento, ma, grazie alle modifiche della geometria strutturale, anche ad un aumento della resistenza alla sollecitazione meccanica.
Come ottimizzare e velocizzare il processo di stesura di un DFM
Lo sviluppo tecnologico ha rivoluzionato completamente il mondo del design, a partire dalla progettazione: se un tempo era necessario un modellista che fosse in grado, attraverso l’uso delle resine, di trasmutare l’idea dalla bidimensionalità della carta alla tridimensionalità del plastico, ora il procedimento è stato reso più semplice dai programmi di progettazione CAD, dai software di simulazione e da una serie di programmi dedicati per affrontare le più differenti tematiche relative al design del prodotto per pressofusione e mass production. Ad esempio è infatti possibile valutare in breve tempo la producibilità dell’oggetto, per poi consultarsi rapidamente riguarda alle modifiche e sottolineare dubbi o criticità emerse dai disegni.
Per ottimizzare e velocizzare questo processo il fonditore può offrire ai proprio clienti un servizio di co-design, nella fase di creazione del prodotto, che possa allineare già dalle primissime fasi di elaborazione del progetto design del prodotto per pressofusione e mass production. Questa fase è antecedente alla stesura e analisi del DFM ed è composta da una serie di attività che hanno come obiettivo quello di aumentare il valore del prodotto e nel contempo ridurne i costi, sia dal lato del prodotto che dal lato del processo di produzione.
Il co-design è quindi la collaborazione tra il cliente e il die caster in un momento importante nella fase di progettazione del prodotto. Infatti, in questa fase, lo scambio di informazioni e di esperienze consente al fornitore di evidenziare i punti critici richiesti dal cliente, quali quelli estetici, funzionali e strutturali per agire direttamente sui disegni in concerto con il cliente.
Riduzione del peso, nessuna lavorazione secondaria, consulenza diretta per le finiture, l’ottimizzazione dello stampo, riduzione di componenti e di costi per l’assemblaggio sono solo alcuni dei vantaggi in un ciclo produttivo che prevede la progettazione, la fusione, le operazioni di lavorazione e l’assemblaggio. Benefici che permettono di risparmiare tempo, materiale e di evitare costi aggiuntivi.
Nel caso quindi di una stratta collaborazione tra il cliente e il fonditore in termini di co-design nella fase di design del prodotto per pressofusione, la fase di stesura e analisi del DFM sarà più veloce ed ottimizzata. Un disegno già ottimizzato per la produzione, già adattato ai processi di mass production, fornirà al cliente un prodotto finale in linea con le sue attese, con meno rischi e meno scarti.
A seguire un breve schema del processo con l’aggiunta della fase di co-design.
Vantaggi del co-design
Processo convenzionale
Processo co-design
I vantaggi offerti dal co-design sono numerosi: potete trovare più informazioni al riguardo nella sezione dedicata del nostro blog.