I trattamenti superficiali nella pressofusione di zinco
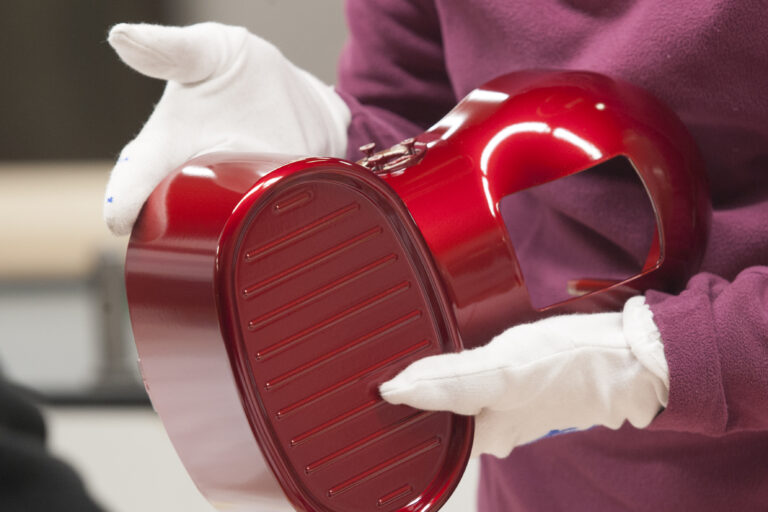
Un approccio verticale alla produzione parte dallo sviluppo del prodotto e dalla definizione del progetto dello stampo, fino ad arrivare alla realizzazione dell’attrezzatura ed alla definizione del processo di pressofusione. Il ciclo produttivo viene quindi completato prevedendo anche una differente gamma di trattamenti e lavorazioni successive che permettono all’azienda produttrice di offrire non solo pressofusi grezzi, ma anche prodotti finiti. Ciò è possibile anche grazie alla collaborazione con partner terzi specializzati.
Nello specifico, questo post è dedicato alla produzione di pressofusi destinati ai trattamenti superficiali di cromatura e di verniciatura.
Cromatura
Un pressofuso cromato presenta importanti caratteristiche estetiche e metallurgiche, che lo rendono tecnologicamente molto interessante. Tale rivestimento permette infatti di conferire al pezzo una vasta gamma di finiture, che ne influenzano profondamente la resa estetica finale: oltre alla cromatura bianca sono ottenibili differenti colorazioni e finiture superficiali (lucida, perlacea o satinata grazie a particolari pretrattamenti). Inoltre, questo trattamento superficiale garantisce al pressofuso una maggiore resistenza ai fenomeni di corrosione, incrementandone anche la resistenza all’abrasione e all’usura superficiale.
Applicare questo trattamento con successo presenta tuttavia sfide non indifferenti: data la reattività della zama ai processi elettrochimici necessari per la cromatura, che avvengono in ambienti acidi, le discontinuità superficiali vengono amplificate e risultano in difettosità che ne compromettono la resa estetica e le proprietà funzionali.
La condizione superficiale richiesta viene spesso raggiunta attraverso trattamenti di pulitura superficiale, avendo cura di non eliminare lo strato a grano fine del pressofuso.
La cromatura risulta pertanto uno dei trattamenti superficiali più difficili da applicare ad un getto in zama: è dunque cruciale un attento design dello stampo e del processo produttivo, che deve essere particolarmente stabile. Il co-design del processo galvanico è inoltre un importante valore aggiunto per ottenere un pressofuso cromato di elevata qualità.
Valenza estetica e funzionale della cromatura
Come anticipato, questo rivestimento può avere due finalità differenti: estetica o funzionale. Nonostante esse non siano necessariamente disgiunte, distinguiamo quindi due processi differenti.
Il primo, per finalità estetiche, prevede la deposizione sulla superficie di zama di tre diversi strati metallici: rame, nickel ed infine un flash di cromo. Il rame alcalino proteggerà la zama dai successivi ambienti acidi, mentre il rame acido (in bagno di acido solforico) uniformerà la superficie e fornirà una base compatibile per il nickel, che garantirà resistenza alla corrosione e una superficie lucida. Infine, un flash di cromo conferirà il colore bianco.
Il processo di cromatura a spessore, per componenti funzionali, prevede invece il deposito diretto di uno spesso strato di cromo sulla superficie di zama. In questi casi lo spessore può superare i 15 micron (un valore decisamente superiore se paragonato ai 0,2 micron della cromatura con funzione estetica). La superficie finale sarà grigia ed opaca, e garantirà ottima resistenza alla corrosione e all’abrasione.
Difettosità riscontrabili in un pressofuso cromato
Soffermiamoci ora su alcune difettosità in particolare, che si possono riscontrare sui pezzi cromati, analizzandone brevemente le cause e le strategie risolutive adottabili, sia in pressofusione, sia durante il trattamento superficiale. Nello specifico, tratteremo le seguenti difettosità:
- Porosità
- Delaminazione
- Solchi
Porosità
Un primo difetto particolarmente diffuso è rappresentato dalla formazione di porosità (anche chiamate vaiolature), ovvero di piccoli crateri circolari (con diametro fino a 0.5mm). Sono solitamente causate da bolle di gas generate durante l’elettrodeposizione non correttamente evacuate, dipendenti da porosità presenti nel substrato di zama, da una superficie non correttamente preparata (con una bagnabilità errata) o da un design non ottimale dei telai. Per evitarle è fondamentale una ottimizzazione del design dello stampo, intervenendo su omogeneità di riempimento e termoregolazione e minimizzando la presenza di zone fredde particolarmente sensibili al difetto. È altresì importante che il processo di stampaggio operi in una condizione di stabilità termica, garantendo pressofusi il più possibile ripetibili per la preparazione successiva. Infine, è bene studiare i telai da utilizzare in galvanica in funzione della geometria del getto, evitando superfici parallele al pelo libero del bagno, per non generare ristagni di bolle di gas.
Delaminazione
Un secondo difetto comune è la mancata aderenza tra i diversi layer, chiamata delaminazione. Essa è causata da porosità intrappolate nel substrato o da fenomeni di corrosione che avvengono tra i diversi strati.
Una corretta analisi della distribuzione delle porosità superficiali è fondamentale per capire come intervenire su stampo e processo produttivo e permetterà di ottimizzare il processo di pulitura e preparazione della superficie. È inoltre importante controllare la stabilità delle condizioni dei bagni galvanici, riducendo i tempi tra le fasi per minimizzare i fenomeni di corrosione.
Solchi
Infine, è possibile riscontrare la presenza di solchi, all’apparenza graffi, su determinate superfici: la loro origine è da ricercarsi in un deposito disomogeneo del rivestimento galvanico che non è in grado di coprire completamente i solchi lasciati dalla lucidatura.
Pur trattandosi di un difetto che non dipende direttamente dal pressofuso (e quindi risolvibile intervenendo sugli spessori depositati e sul design dei telai), anche in questo caso si evidenzia l’importanza di un approccio verticale per ottimizzare il prodotto finito: una superficie del getto omogenea richiederà una lucidatura meno invasiva.
Verniciatura
Un ulteriore trattamento superficiale è la verniciatura.
Similmente alla cromatura, l’applicazione di un film sulla superficie di un pressofuso da un lato conferisce una maggiore resistenza a fenomeni corrosivi e di usura, e dall’altro ha un ruolo fondamentale nel definire le caratteristiche visive finali del prodotto, colore e texture. La finalità è quindi duplice: funzionale e decorativa.
Pur tollerando una condizione superficiale del pressofuso più disomogenea (non è prevista infatti una preparazione meccanica della superficie prima dell’applicazione del rivestimento), la verniciatura di un pressofuso in zama presenta specifici requisiti e difettosità.
Tipologie di verniciatura
Fra i processi di verniciatura più comuni ricordiamo la verniciatura a liquido, che permette di contenere gli spessori depositati e la temperatura di indurimento. Nella verniciatura a polvere, invece, il pigmento viene applicato in forma di polvere sul pezzo e quindi indurito, ottenendo un rivestimento spesso e robusto. Infine, nel processo elettrochimico di cataforesi, il pigmento è depositato immergendo il pezzo in appositi bagni (come nel processo galvanico), garantendo così la copertura di tutte le superfici del pezzo (e non solo quelle raggiungibili con una pistola).
Difettosità riscontrabili in un pressofuso cromato
Buccia d’arancia
Uno dei difetti più comuni del processo di verniciatura è una superficie irregolare detta buccia di arancia, dovuta ad un deposito di vernice eccessivo, o ad una distanza pezzo-ugello ridotta.
Tale difettosità può essere risolta principalmente definendo correttamente i parametri di verniciatura (automatizzando il processo) e migliorando la qualità superficiale del getto, riducendo la presenza di marezzature, sfogliature.
Schivature
Un secondo difetto comune sono le schivature (o occhi di pernice), che si presentano come piccoli crateri (0,2-0,4 mm) dove la vernice non riesce ad aderire.
La mancata adesione è solitamente dovuta ad una contaminazione della superficie di zama da residui oleosi o dei prodotti di verniciatura da additivi siliconici.
Un approccio statistico all’analisi del processo, con l’ausilio di un piano sperimentale ben strutturato, permette di approcciare un fenomeno complesso che coinvolge due tecnologie differenti, identificando le variabili fisiche che influenzano la formazione del difetto per ottimizzare il risultato.
Blistering
Un ulteriore difetto rilevante è quello del blistering: gas o aria intrappolati nel pressofuso, espandendosi durante la cottura della vernice, possono portare alla formazione di “bolle”, ovvero a deformazioni rigide della superficie del pezzo, specialmente in corrispondenza di pareti sottili.
Questo fenomeno è difficilmente risolvibile in verniciatura (le temperature e i tempi di indurimento sono legate al tipo di vernice utilizzata). Diventa quindi fondamentale ottimizzare il processo di riempimento dello stampo, definendo il design più adeguato dei canali anche con l’ausilio dei software di simulazione CFD, al fine di minimizzare le turbolenze che portano ad intrappolamenti di aria. Inoltre, l’adozione di un sistema per lo stampaggio sottovuoto aiuta fortemente a ridurre l’incidenza di questa anomalia.