Progettazione di uno stampo per pressofusione
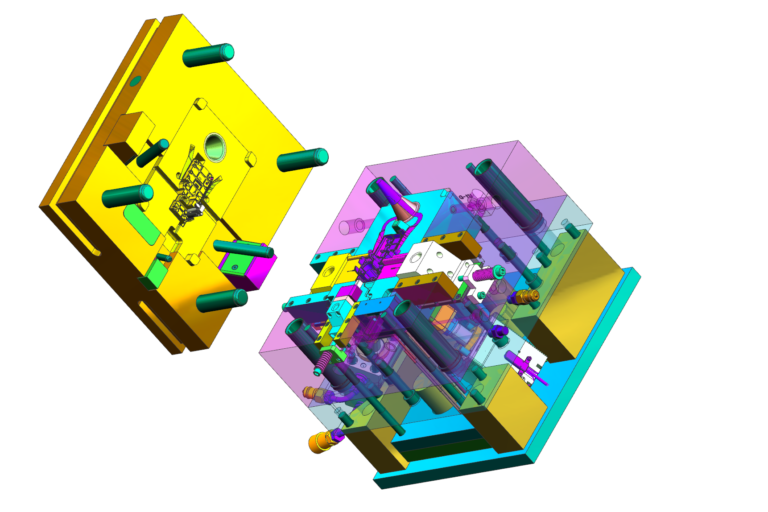
In questo post parleremo del processo di progettazione di uno stampo per pressofusione ad alta pressione, elencando le fasi principali che lo compongono.
Fase preliminare
Prima di cominciare la progettazione di uno stampo, è necessario accertarsi della producibilità del pezzo tramite stampaggio a pressofusione. In questa fase sono due i punti da tenere in considerazione: la fattibilità del processo da un punto di vista dimensionale e geometrico:
- Le dimensioni del componente da realizzare e il numero di figure che dovremmo ottenere ad ogni stampata permettono di calcolare il volume dell’intero getto e l’area di spinta. Questi due dati si rendono indispensabili nello studio di fattibilità del processo.
- La geometria del componente da realizzare deve prevedere la modellazione di una linea di divisione stampo per la quale le inclinazioni delle superfici siano orientate secondo la direzione di estrazione (sformo delle figura). Inoltre, le tolleranze geometriche delle quote, indicate nel modello 2D o dal cliente, possono essere più o meno difficili da realizzare a causa del fenomeno del ritiro per raffreddamento del getto (precisione realizzativa tecnologica). Quote con tolleranze identiche possono essere più o meno critiche a seconda del loro valore nominale: maggiore è il valore nominale di una quota e maggiore sarà la difficoltà a raggiungere quel valore sul getto a causa del ritiro. Questa viene definita “precisione realizzativa” ed è caratteristica di ogni processo tecnologico.
Per queste ragioni può essere utile accordarsi con il proprio cliente per lavorare al progetto con una logica di co-design, in modo da poter trovare un comune accordo sulle modifiche da applicare alle tolleranze critiche, alla geometria del componente e alla posizione delle linee di chiusura stampo.
Una volta valutata la producibilità del pezzo, è possibile passare alla progettazione dello stampo per pressofusione vera e propria. Come è logico supporre, la progettazione dello stampo parte dalla conoscenza e dalla definizione del pezzo che dovrà essere stampato.
Per entrare in profondità nell’analisi e nel dettaglio delle diverse fasi progettuali è necessario riconsiderare i dati ricavati precedentemente riguardo al peso (o volume) del pezzo, alla sua area di proiezione in direzione dell’apertura stampo, e al numero di cavità previste.
Numero di impronte
Il numero di cavità dipende dall’ipotesi dei ritmi produttivi, ovvero da quanti pezzi sarà necessario produrre e dal loro orientamento: si potrà quindi decidere di avere uno stampo a impronta singola o multi-impronta.
Nel caso di uno stampo per pressofusione a multi-impronta, è necessario tenere a mente l’aumento del grado di complessità delle fasi di riempimento ed estrazione, la disposizione delle figure ed il fatto che maggiori sono le dimensioni del pressofuso e più difficile risulta la gestione del processo produttivo e del prodotto. Basti pensare che, anche solo dal punto di vista logistico, l’aumento del numero di impronte è direttamente proporzionale al flusso di materiale da movimentare.
L’area di proiezione
L’area di proiezione identifica la superficie fittizia che è possibile ricavare dalla proiezione della cavità sul piano ortogonale alla direzione di apertura dello stampo, e ricopre un ruolo fondamentale in fase di progettazione: da essa dipende infatti la forza generata dal metallo sulle pareti dello stampo. In base alla dimensione della forma e al suo orientamento, interverranno forze minori o maggiori in fase di riempimento. Una forza eccessiva potrebbe portare ad una fuoriuscita del materiale, e quindi alla formazione di bave lungo il profilo. Se le forze sono troppo elevate rispetto alla capacità di chiusura della pressa è possibile superare il limite stampaggio con conseguente impossibilità di produrre con quello stampo.
Per evitare che ciò accada, si procede solitamente ad un calcolo della forza massima generata dal metallo durante il riempimento. La forza massima deve quindi essere uguale al prodotto dell’area di proiezione per la pressione specifica massima producibile dalla macchina, moltiplicata per un opportuno il coefficiente di sicurezza.
Questo coefficiente considera la spinta dinamica del metallo. La sua funzione è principalmente quella di offrire un ampio margine per contenere il cosiddetto colpo di ariete, ovvero il momento di massima pressione alla fine del processo di riempimento. La pressa scarica infatti a fine processo sia una forza statica che una forza dinamica, causando un picco di pressione che deve essere assorbito dalla forza di chiusura della macchina.
La forza di chiusura stampo espressa dalla pressa dipende dal modello di pressa che si andrà ad utilizzare e dal diametro del suo pistone.
La spinta del metallo e quindi l’area di proiezione è uno dei principali vincoli da considerare durante la progettazione di uno stampo per pressofusione.
Volume e forma dello stampo
Come già accennato, lo spazio volumetrico del pezzo è fondamentale per la progettazione degli stampi per pressofusione. Oltre al volume complessivo è necessario tenere bene a mente che componenti massivi e di grandi dimensioni subiranno anche un ritiro maggiore, dovuto all’incremento del coefficiente di ritiro in funzione di tempi di raffreddamento più laschi, e che quindi le cavità dello stampo dovranno essere dimensionate di conseguenza.
Inoltre, è necessario considerare una serie di variabili che andranno ad influire sulla dimensione finale dello stampo. Tra queste ricordiamo le dimensioni degli attacchi di colata, il tipo di chiusura stampo, la dimensione dei canali e delle uscite e la presenza di masse di scarico.
- Il tipo di chiusura stampo più semplice è quello apri-chiudi, per il quale la linea di chiusura pezzo è una sola e la più semplice possibile. Questo sistema funziona per pezzi dalle geometrie semplici, che possono essere svincolate dallo stampo semplicemente grazie al movimento di allontanamento dei piani macchina e all’estrazione, ma non può essere applicato per strutture con forme sottosquadra o con geometrie particolari, che necessitano invece di movimenti trasversali o inclinati rispetto alla direzione di apertura. In questi casi lo stampo dovrà tenere conto delle necessarie dimensioni dei carrelli e dei loro movimenti.
-
- La dimensione dei canali di iniezione è dipendente dalla posizione degli attacchi di colata, da quella del pezzo e dal numero di cavità. La loro forma deve rispettare delle esigenze di fluidodinamica: ad esempio, essa è caratterizzata da una sezione decrescente nella direzione di moto del metallo fuso, per facilitarne l’adesione alle pareti dello stampo. Questo restringimento progressivo permette di ottenere un flusso in accelerazione e di sfavorire il distacco di strato limite dalle pareti del canale. La velocità aumenta fino all’ingresso del metallo nella cavità del pezzo, creando un effetto di nebulizzazione del metallo. Lo strato limite più uniforme evita la formazione di turbolenze che potrebbero provocare dei ristagni di materiale o di aria e, talvolta, anche l’erosione dello stampo.
-
- Le masse di scarico sono simili a pozzetti posizionati in punti strategici dello stampo e svolgono due funzioni principali: la prima è di raccogliere il primo fronte di metallo, che è solitamente più freddo del resto del flusso. In questo modo si evita la formazione di giunture fredde e altri difetti qualitativi del pressofuso, migliorandone la compattezza e la qualità superficiale. La seconda funzione riguarda invece la temperatura lo stampo: raccogliendo il materiale fuso si generano delle sorgenti di calore che incrementano la temperatura dello stampo nelle zone di maggiore criticità qualitativa e riducono il transitorio termico.
-
- Un altro elemento che influisce sulla dimensione dello stampo è la posizione dei canali del sistema di evacuazione dell’aria. Questi canali dalla geometria particolare, detti sfiati, permettono all’aria di fuoriuscire dallo stampo, riducendo quindi intrappolamenti di aria nel metallo.
Una volta definite posizioni e dimensioni di tutti questi elementi dello stampo per pressofusione, è possibile passare alla fase successiva.
Simulazione tramite modelli semi-empirici
Completato il design iniziale dello stampo, è possibile procedere ad una simulazione del riempimento pezzo tramite l’utilizzo di modelli semi-empirici.
Queste simulazioni servono per calcolare la modalità ideale di riempimento dello stampo: a seconda della funzione del pezzo che si dovrà stampare, infatti, il sistema di riempimento può variare. Nelle componenti che avranno una funzione strutturale sono da prediligere aspetti come la resistenza meccanica e la compattezza, mentre per le componenti puramente estetiche sarà necessario assicurarsi la migliore finitura superficiale possibile, evitando quindi ogni porosità superficiale e anche intrappolamenti di aria che potrebbero fuoriuscire durante i trattamenti successivi, danneggiando lo strato di trattamento superficiale.
Variando il tempo di riempimento è possibile variare queste caratteristiche: più il riempimento sarà veloce, maggiore sarà la qualità superficiale; al contrario, maggiore sarà il tempo e la pressione, maggiore sarà la robustezza del pezzo.
Terminate queste analisi sarà possibile individuare preventivamente eventuali problemi nella fase di stampaggio e quindi re-intervenire sul design dello stampo prima di produrlo.
Riassumendo, il design di uno stampo per pressofusione parte da una verifica della producibilità del pezzo, passa per il calcolo delle forze di spinta del metallo e, successivamente, per il posizionamento dei canali di riempimento, sfiato e dei necessari carrelli e movimenti. Il design e l’ottimizzazione delle cavità quali canali di iniezione, sfiati e fagioli può essere realizzato con l’aiuto di un software di simulazione per valutare il sistema di riempimento ideale ed evidenziare eventuali problematiche. Una volta concluse queste fasi, è possibile passare alla produzione dello stampo progettato.