Pressofusione dello zinco per piccoli elettrodomestici: componenti per macchine del caffè
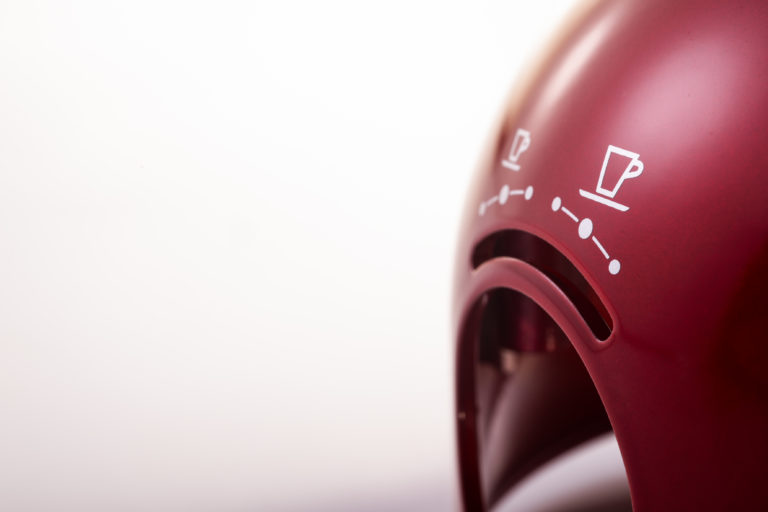
Lo zinco è un materiale che può essere impiegato in diversi ambiti industriali, tra i quali figura il settore dei piccoli elettrodomestici. Nel seguente articolo verranno descritti i principali vantaggi dell’utilizzo dello zinco per la produzione di componenti di piccoli elettrodomestici, in particolare di macchine del caffè.
1. Libertà di design
Lo zinco, più specificatamente le leghe Zama, è un materiale che consente di produrre componenti aventi molteplici tipologie di forme. Grazie allo zinco è infatti possibile ottenere superfici molto sottili, che non potrebbero essere ottenute utilizzando altri materiali, come l’alluminio. Ciò si traduce in una più ampia libertà di design nella progettazione di un componente, con conseguente singolarità e unicità del pezzo prodotto. Lo zinco rappresenta così un ottimo metallo da utilizzare per la produzione di componenti complessi dal punto di vista della forma. Nella tabella sottostante sono riportati i valori di spessore minimo ottenibile di zinco e alluminio:
Proprietà | Unità di misura | ZP3 | ZP5 | ZP2 | ZP8 | LM24 | A380 |
---|---|---|---|---|---|---|---|
Spessore minimo ottenibile | mm | 0,4 | 0,4 | 0,4 | 0,4 | 1,3 | 1,3 |
Scegliendo lo zinco per la produzione di piccoli elettrodomestici è possibile ottenere numerosi vantaggi relativi alla qualità dei componenti, dal momento che le leghe di zinco presentano un ritiro stabile e un’elevata resistenza. Per esempio, rispetto ai materiali plastici, lo zinco ha una tolleranza migliore e un carico di snervamento e di rottura superiore (Tabella 1): queste caratteristiche permettono di ottenere una maggiore libertà di design e notevoli qualità del prodotto finito.
Proprietà | Unità di misura | ZP3 | ZP5 | ZP2 | ZP8 | ABS | NYLON PA66 | NYLON PA66 30% GR | POLICARBONATO | ACETAL |
---|---|---|---|---|---|---|---|---|---|---|
Tolleranze su 100 mm | +/- µ | 100 | 100 | 100 | 100 | L’alto valore di ritiro e l’umidità non consentono strette tolleranze nella plastica | ||||
Carico di snervamento | MPa | 268 | 295 | 361 | 319 | n/a | n/a | n/a | n/a | n/a |
Carico di rottura | MPa | 308 | 331 | 397 | 387 | 25-65 | 71-85 | 155-210 | 54-72 | 37-70 |
Tabella 1 – Valori di tolleranza, carico di snervamento e carico di rottura di zinco e materie plastiche
2. Trattamenti estetici di alta gamma
Alle leghe di zinco possono essere applicati numerosi trattamenti superficiali. Nello specifico, è possibile migliorare le caratteristiche estetiche dei componenti attraverso trattamenti che trasformano l’oggetto e ne migliorano la finitura. I principali trattamenti estetici realizzabili sullo zinco sono:
- Trattamenti galvanici: cromature lucide, cromature satinate, rivestimenti galvanici di diverso colore
- Verniciature a liquido
- Verniciature a polvere
- Trattamenti speciali per evitare l’usura del materiale
Inoltre, sui componenti in zinco è possibile effettuare specifici trattamenti che sfruttano le caratteristiche fisiche della lega. Tra i trattamenti sopracitati, la verniciatura a polvere costituisce un eccellente esempio di trattamento estetico ottenibile attraverso un processo di deposizione elettrostatica della polvere e di successiva cottura ad elevata temperatura (circa 200°C). Questa tipologia di verniciatura permette di ottenere una migliore texture al tatto rispetto alla classica verniciatura a liquido. Eseguire questo trattamento su un componente in zinco gli conferisce un importante valore aggiunto.
I trattamenti dei materiali solitamente seguono i trend del settore di rifermento: per soddisfare questa mutevole esigenza esiste una varietà infinita di soluzioni che si applicano allo zinco.
3. Supporto del fornitore
Un cliente che si affida a un fornitore di zinco qualificato può trovare nella sua esperienza verticale la capacità di lavorare anche sul design e di consigliare al cliente geometrie innovative e finiture speciali. Questo servizio, denominato co-design, è la collaborazione tra cliente e fornitore volta alla realizzazione di un prodotto con specifiche funzioni e caratteristiche meccaniche, che sia allo stesso tempo conforme al processo di produzione. Il co-design può aiutare i designer a comprendere nel dettaglio le caratteristiche dello zinco e a sfruttare appieno il know-how del proprio fornitore. Lo zinco è un materiale versatile che consente di sperimentare con forme e design, permettendo così la concezione e la creazione di pezzi unici. Dal momento che la pressofusione di zinco rappresenta un mercato estremamente verticale, i suoi fornitori hanno una profonda conoscenza verticale della materia e possono supportare i clienti nella produzione di pezzi esclusivi.
L’adattabilità delle leghe di zinco si dimostra particolarmente utile nell’ambito dei piccoli elettrodomestici: mentre altri prodotti sono più standardizzati e la progettazione creativa è limitata, i piccoli elettrodomestici si rivelano un prodotto appropriato per testare la versatilità dello zinco. Essendo composti da molteplici componenti, per i piccoli elettrodomestici è possibile immaginare un’ampia varietà di soluzioni con l’utilizzo di leghe di zinco, migliorando in questo modo l’aspetto, la performance e l’unicità del prodotto.
4. Customer experience
Quando si seleziona un materiale un ulteriore aspetto che deve essere tenuto in considerazione è la cosiddetta customer experience, ovvero l’esperienza del consumatore. La relazione tra consumatore finale e prodotto è costituita da numerose variabili, come performance e utilità, ma anche aspetto visivo, texture e resistenza. I componenti in zinco trasmettono eccellenti percezioni in termini di impatto visivo e sensazione al tatto. Un prodotto realizzato in zinco ha maggiori probabilità di essere percepito come pulito, resistente e di ottima qualità.
In merito a queste caratteristiche, è bene tenere a mente che il fruitore ha accesso all’utilizzo della macchina attraverso maniglie e tasti. Se il corpo del prodotto è realizzato in plastica, la maniglia o il tasto dovrebbe essere realizzato in zinco, in modo da offrire all’utilizzatore una diversa esperienza nella fruizione del prodotto. Questi dettagli potenziano la customer experience e fanno la differenza per la scelta del consumatore.
5. Pulizia dei componenti
Dal punto di vista del consumatore finale poter pulire in modo facile e veloce un prodotto costituisce un aspetto rilevante, che influenza la scelta d’acquisto. Per esempio pulire componenti in zinco cromato è più facile rispetto ad altre superfici, perché presentano una superficie dura, compatta e liscia. Un prodotto con queste caratteristiche semplifica il processo di pulizia, rendendolo più rapido ed efficace: ciò si traduce in un vantaggio per il consumatore. Non solo i componenti in zinco cromato sono più semplici da pulire, ma trasmettono anche una sensazione di pulizia e lucentezza che ha un forte impatto sull’occhio del consumatore. Grazie a queste qualità i componenti in zinco risaltano a confronto con altre superfici.
6. Riciclabilità dello zinco
Sempre più aziende virtuose sono alla ricerca di sostenibilità. In questa ottica di sviluppo sostenibile è consigliabile utilizzare materiali riciclabili, tra i quali figura lo zinco. Le leghe di zinco possono essere riutilizzate e fuse numerose volte senza che ciò intacchi le loro proprietà. Generalmente l’utilizzo di leghe di zinco riciclate viene limitato approssimativamente al 50%: ciò permette di esaurire completamente gli scarti di produzione. Oggigiorno l’attuazione di questo sistema di riciclaggio permette di riciclare una grande quantità di scarti provenienti dalla pressofusione dello zinco. Lo zinco rappresenta un materiale con una ridottissima tossicità, che prevede un basso consumo energetico per la sua produzione e riciclabile. Queste proprietà rendono lo zinco un materiale environmentally friendly.
7. Lead time ridotto
Il lead time è il periodo di tempo che un’azienda necessita per soddisfare la richiesta di un cliente in termini di offerta. Logicamente, un breve periodo di tempo si traduce in risultati più rapidi e clienti più soddisfatti. Al fine di conseguire questa condizione, lo zinco rappresenta un ottimo materiale grazie al suo breve tempo ciclo. Infatti, il lead time è un concetto correlato al tempo ciclo, cioè il periodo di tempo richiesto per completare la produzione di un prodotto. Considerando il tempo ciclo di un prodotto è così possibile supporre il relativo lead time. Scegliendo lo zinco invece di altri materiali, come l’alluminio e la plastica, il lead time verrà ridotto, determinando un servizio più rapido ed efficiente.
I tempi ciclo legati allo stampaggio delle leghe di zinco sono, infatti, inferiori rispetto a quelli delle leghe di alluminio e delle materie plastiche. Nel primo caso, l’alluminio viene stampato a temperature notevolmente superiori, quindi il tempo ciclo risulta maggiore a causa dei tempi di raffreddamento. Per quanto riguarda la plastica, questa presenta invece dei tempi di riempimento superiori.
Proprietà | Produttività tipica | Range di produttività |
---|---|---|
Unità di misura | Cicli/ora | Cicli/ora |
ZP3 | Grandi 200-500. Medi 400-1000. Piccoli 2000-3000 | 200-3600 |
ZP5 | ||
ZP2 | ||
ZP8 | ||
LM24 | 50-250 | 30-350 |
A380 | ||
ABS | La produttività è condizionata dalla taglia del prodotto, dal materiale usato e dal tempo di raffreddamento | Stampaggio ad iniezione: da 100 a 400 cicli/ora |
NYLON PA66 | ||
NYLON PA66 30% GR | ||
POLICARBONATO | ||
ACETAL |
Tabella 2 – Produttività tipica e Range di produttività di zinco, alluminio e materie plastiche
CASE STUDY N. 1
La Bruschi produce numerosi componenti per macchine del caffè. In questo particolare caso l’azienda è stata contattata per realizzare un vassoio porta tazza per una macchina del caffè. Il vassoio è interamente realizzato in zinco e integralmente cromato. Tutta la superficie del componente è considerata superficie estetica, poiché l’esterno è visibile all’occhio dell’utilizzatore e l’interno diventa visibile nel momento in cui viene rimosso il coperchio in plastica ed è possibile accedere alla parte interna del vassoio e pulirla.
Il processo di cromatura prevede delle fase preliminari per la preparazione del pezzo. In particolare, il componente deve essere pulito e lucidato tramite l’impiego di rulli, nastri e materiale abrasivo. Il componente necessita di essere pulito anche internamente, per questo motivo la Bruschi ha ideato delle modifiche al processo tecnologico che hanno permesso di ottenere un risultato equivalente.
La Bruschi è così riuscita a creare un vassoio porta tazza in Zama, cromato esternamente e internamente.
CASE STUDY N. 2
In questo secondo caso il cliente ha richiesto alla Bruschi la produzione di manopole cromate per macchine del caffè. La difficoltà di realizzare questo componente risiede nella geometria, nella produttività e nella qualità superficiale. La manopola costituiva un componente particolarmente critico perché il layout delle cavità dello stampo standard di produzione delle maniglie non permetteva di raggiungere i livelli di produttività e di costi richiesti dal cliente. Grazie all’esperienza e alle competenze dei designer della Bruschi, l’azienda ha ideato un metodo alternativo per alimentare lo stampo: i designer hanno così progettato un nuovo stampo che consentisse di rientrare nei parametri richiesti. Infatti, grazie al nuovo layout si sono ridotti sia i costi che i livelli di produttività.
In conclusione, l’utilizzo dello zinco per la produzione di componenti di macchine del caffè apporta notevoli vantaggi. Prediligendo l’impiego di zinco è infatti possibile progettare e creare un prodotto funzionale ed estetico, capace di coniugare libertà di design e trattamenti estetici di alta gamma e che al contempo tenga conto delle variabili di produzione e di costi.
Se desideri essere aggiornato sulle novità del mondo della pressofusione in lega di zinco, iscriviti al nostro blog.