Il controllo qualità nella pressofusione di leghe di zinco
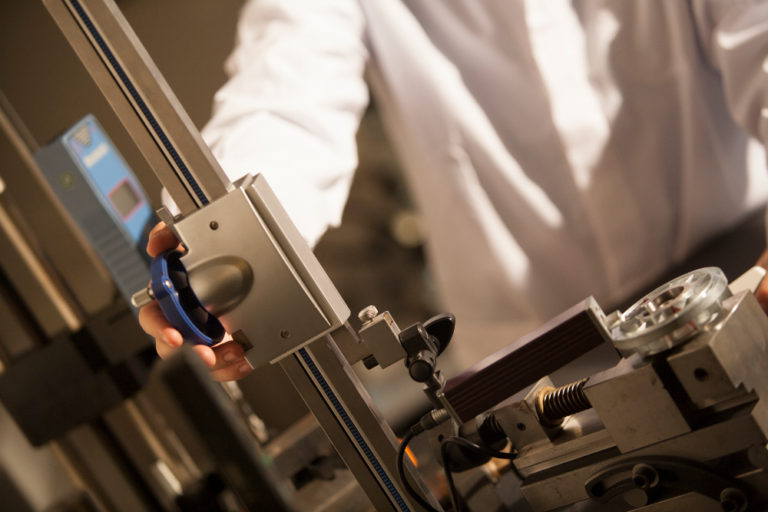
Questo post è dedicato ad analizzare le attività del controllo qualità nella produzione di pressofusi in lega di zinco: una serie di operazioni fondamentali che accompagnano tutte le fasi di un progetto.
Nel dettaglio, dopo aver dato una definizione di controllo qualità, approfondiremo il lavoro del reparto nelle diverse fasi produttive per poi indagare le attività che accompagnano la mass production. Infine, dedicheremo qualche riga all’analisi dei vantaggi che una corretta implementazione del controllo qualità può apportare.
Definizione di controllo qualità
In un’azienda manifatturiera il controllo qualità è costituito dall’insieme delle attività effettuate per verificare il rispetto delle richieste del cliente nella realizzazione di un prodotto. Allo stesso tempo, però, è chiamato allo stesso modo anche il team impegnato in queste verifiche: per questo, nel corso dell’articolo, ci riferiremo ad entrambi questi enti come controllo qualità.
Per un approfondimento su questi temi consigliamo di visitare il sito Qualitiamo, un portale interamente dedicato alle tematiche della qualità e delle sue certificazioni.
Nel campo della pressofusione di leghe di zinco istituire un team specializzato che si dedichi esclusivamente alla verifica della qualità si è reso necessario con l’evoluzione del mercato e dei prodotti. Infatti il rispetto delle quote e dei parametri richiesti dal cliente può essere garantito esclusivamente dall’operato di personale specializzato e che, al di fuori dei tempi di produzione, effettui tutte le verifiche necessarie.
Dopo queste necessarie premesse analizziamo ora le fasi della produzione di un pressofuso in lega di zinco indagando, di volta in volta, le attività intraprese dal controllo qualità.
Fasi del controllo qualità
Il controllo qualità accompagna, come già scritto, il componente in tutte le fasi della sua produzione: è necessario che questo ente presidi la progettazione, la campionatura e la produzione di massa fino all’arrivo dei componenti presso fornitori esterni e presso il cliente. Esploriamo allora le attività di questo importante reparto in ogni fase della vita di un progetto.
Progettazione
Tutte le attività che il controllo qualità effettua nel corso della produzione hanno avvio in questa fase. Durante la progettazione, infatti, il team deputato alla qualità interviene insieme agli altri reparti per valutare la fattibilità del prodotto. In questa fase si analizzano le specifiche Cliente in merito di documentazione richiesta in fase di qualifica prodotto: FMEA, piani di controllo, analisi di riproducibilità delle misure, gage R&R vengono valutati per individuare criticità e gap rispetto alle specifiche del Cliente. Inoltre, è in questa fase in cui si inizia a redigere le schede di controllo e cioè lo strumento del quale si servirà il team del controllo qualità in fase di produzione.
Campionatura
In fase di campionatura vengono effettuate le verifiche richieste dal cliente sui primi pezzi realizzati. Queste verifiche comprendono controlli dimensionali, funzionali ed estetici (se richiesti). Quindi, una volta acquisite tutte le informazioni necessarie si compila la parte documentale necessaria per l’approvazione del prodotto in ottica industriale. I campioni vengono così inviati al cliente per una valutazione puntuale. Al ricevimento del benestare si passa quindi alla produzione di massa.
Il controllo qualità della campionatura è fondamentale, sia internamente sia lato cliente, perché è in questa fase che si creano i prodotti approvati ed esemplificativi del processo standard che sarà ripetuto in fase di produzione di massa.
Produzione
Durante la produzione vengono effettuati i controlli qualitativi previsti dalle schede di controllo. È in questa fase che si innesta il lavoro dei controllori e del team qualità.
Un semplice controllo da parte dell’operatore a bordo macchina, sui componenti in produzione e sui bancali finiti, non è sempre sufficiente a garantire il rispetto dei requisiti qualitativi richiesti dal cliente.
Il team qualità, dopo aver attivamente partecipato alla progettazione e alla campionatura, entra in gioco anche all’avviamento della produzione. Infatti, i primi componenti stampati vengono prelevati, misurati e testati. In seguito l’operatore a bordo macchina effettua un controllo per ogni unità di imballo ma il team interviene periodicamente, sulla base di una frequenza concordata con il cliente o stabilita internamente, per prelevare campioni ed eseguire i test contenuti nella scheda di controllo.
Il fine dei controlli periodici non è solo quello di verificare il rispetto dei requisiti del cliente e la mancanza di non conformità ma anche quello di monitorare l’andamento della produzione. L’inserimento dei dati raccolti in un database permette infatti di creare un storico della produzione: una mole di dati importante che permette di prevedere in anticipo le eventuali non conformità e di conoscere le strategie già impiegate per porvi rimedio.
In questa fase il team basa le proprie attività sulla scheda di controllo realizzata in fase di avviamento del progetto e che riporta tutti i requisiti contenuti nel PAPP. Sulla scheda è riportata una fotografia del prodotto con indicazione delle zone critiche, del tipo di controllo da effettuare e degli strumenti che devono essere utilizzati. Sono proprio i dati contenuti nelle schede di controllo che permettono l’aggiornamento del database e la creazione dello storico delle eventuali non conformità.
Dopo aver descritto le fasi in cui subentra il controllo della qualità e le procedure messe in atto per garantire la conformità dei pezzi alle richieste del cliente analizziamo i vantaggi di questo sistema.
Fasi successive alla produzione
Le attività del controllo qualità non si concludono con la produzione di massa: nel processo possono subentrare infatti fornitori esterni e, in questo caso, si rende necessario istituire appositi controlli non solo sul materiale in entrata e in uscita, ma anche sul processo produttivo dei fornitori stessi. È infatti necessario, per garantire il rispetto dei parametri richiesti dal cliente, controllare e garantire la ripetibilità della qualità della merce e dei processi del fornitore. Ovviamente il controllo è posto in essere su tutta la merce elaborata dalla supply chain ma, come precedentemente esposto, è tutto il sistema qualità che dovrà ciclicamente essere verificato e approvato secondo rigidi standard interni oppure esterni.
Infine, il controllo qualità del produttore di pressofusi in lega di zinco è in costante contatto e comunicazione con il controllo qualità del cliente. I due enti, infatti, si scambiano informazioni in merito alla qualità delle forniture e alle attività necessarie per continuare a garantire gli standard attesi.
Vantaggi
Un primo vantaggio, evidente, è la riduzione delle non conformità. È tuttavia importante sottolineare come questo risultato non venga ottenuto solo grazie a controlli accurati eseguiti da personale specializzato ma anche grazie al lavoro che accompagna ogni fase del progetto.
In fase di progettazione è infatti l’incontro di diverse expertise che permette di creare schede di controllo davvero accurate, che implichino lo studio e la previsione dei processi e la costruzione di scenari produttivi realistici. Una buona progettazione delle schede di controllo consente poi di effettuare, in fase di produzione di massa, delle verifiche davvero efficaci e di inserire nel database i dati che permetteranno di prevedere il verificarsi di non conformità e di implementare strategie di arginamento basate su dati ed esperienza.
Lo scambio di informazioni cross funzionale non avviene poi solo in fase di progettazione ma durante la produzione di massa e alla sua conclusione, nel corso di incontri quotidiani in cui si riuniscono i diversi reparti. Grazie alle segnalazioni del controllo qualità infatti, il materiale fermato per non conformità prima di essere smaltito è reso oggetto di una riflessione che coinvolge progettazione, fonderia e qualità.
Nel corso di questi incontri le non conformità sono quindi analizzate e si intraprende un’analisi delle cause, dei fattori di rischio e delle azioni di prevenzione o contenimento che sono state messe in atto.
Il team di controllo qualità quindi è il perno attorno al quale ruotano questi incontri ed è il motore che spinge i diversi reparti a muoversi nella direzione del miglioramento continuo e dello scarto zero, obiettivo che è possibile raggiungere solo con azioni preventive, e non con azioni reattive.
Infine, la creazione e la gestione del database, con le schede di controllo costantemente aggiornate, di operare con consapevolezza e di portare avanti una riflessione sulle cause delle non conformità e sull’efficacia delle strategie di volta in volta adottate. È la conoscenza del passato, infatti, la migliore strategia per prevedere, e migliorare, il futuro.
Conclusioni
Con questo post sulle attività e sui vantaggi del controllo qualità speriamo di essere riusciti a dimostrare come un metodo efficace e risolutivo per la diminuzione delle non conformità sia basato non solo sulla fase di controllo ma anche, e soprattutto, su processi che coinvolgono professionalità e funzioni afferenti a diversi ambiti. Infatti è solo attraverso la condivisione di expertise e il confronto tra i diversi reparti che, grazie all’apporto specifico di ognuno, è possibile raggiungere risultati competitivi.