5 Case Study: guarda i video di pressofusione Bruschi
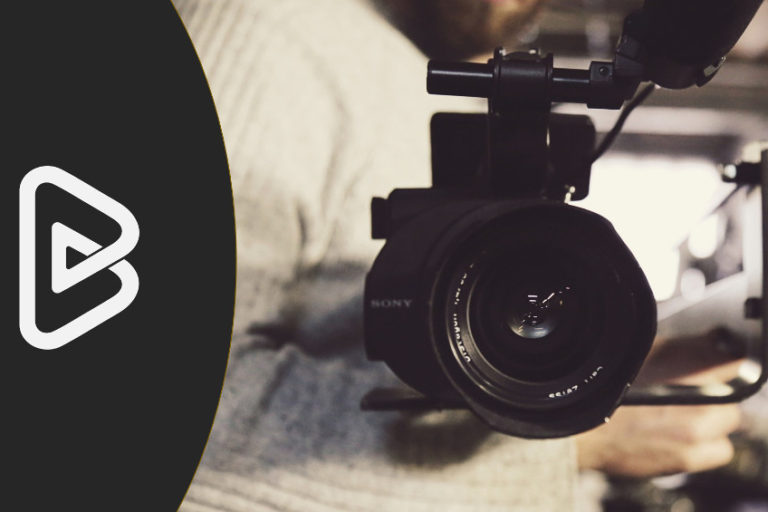
Nell’ultimo anno abbiamo realizzato nuovi video che illustrano il processo produttivo e le caratteristiche di alcuni componenti.
I prodotti sono stati scelti sulla base di diversi principi: si è privilegiata la varietà, selezionando componenti destinati a settori diversi e la complessità, cercando di trasmettere la nostra expertise e competenza nel soddisfare le richieste del cliente.
I video che vi presentiamo sono:
- Pressofusione per piccoli elettrodomestici: macchine del caffè
- Pressofusione per il settore automotive: bloccasterzo elettronico
- Pressofusione per il settore automotive: tetti panoramici
- Pressofusione per porte e finestre: meccanismo di apertura
- Pressofusione per grandi elettrodomestici: cerniera per lavatrici
E ora lasciamo la parola ai nostri esperti.
Pressofusione per piccoli elettrodomestici: macchine del caffè
Nel video è illustrata la produzione di un componente per macchine del caffè e si descrivono le soluzioni tecniche adottate per ottenere una cromatura perfetta.
Questo prodotto è la sezione inferiore di una macchina del caffè destinata al mercato consumer, è un pezzo estetico che entra in vista e contatto con il cliente finale; proprio per questa ragione ci sono specifici aspetti tecnici e qualitativi da considerare. In fase di analisi, infatti, sono emerse difficoltà tecnologiche e di processo, dovute alla forma particolare del componente, che avrebbero potuto inficiare il rispetto degli standard richiesti andando a diminuire la qualità della cromatura.
È proprio la particolare geometria del pezzo a non permettere la lavorazione della superficie interna, ed è per questa ragione che, dopo accurate analisi del processo e riflessioni sulla sagoma del componente, si è scelto di ottenere una superficie che già da grezza fosse adatta al processo di cromatura.
Per il raggiungimento dell’obiettivo sono state intraprese attività di simulazione e prototipazione virtuale e fisica che hanno consentito di definire parametri ottimali per la produzione del pezzo. Grazie alla simulazione e alla prototipazione sono state individuate due proprietà sulle quali lavorare maggiormente: rugosità e qualità superficiale. Per raggiungere già in fase di stampata il risultato atteso si è cercato di sfruttare al meglio i parametri di produzione. La lappatura della matrice è stata la soluzione scelta per ottenere la rugosità superficiale già durante la fase di stampaggio; simulazione e test in produzione ci hanno invece permesso di modificare lo stampo per raggiungere la qualità superficiale richiesta e gli standard previsti.
L’adozione di queste soluzioni tecniche e il cambio dei parametri hanno quindi consentito di ottenere un prodotto adatto a ricevere trattamenti di pulitura e cromatura. La fase di pulitura è effettuata sui pezzi ancora grezzi la cui superficie esterna viene levigata perché il successivo trattamento di cromatura abbia un buon risultato. La fase successiva è, appunto, la cromatura. La cromatura è un processo galvanico estetico che conferisce ai pressofusi un aspetto accattivante e protettivo: la superficie cromata protegge infatti dalla corrosione. È un processo composto da più passaggi durante il quale i prodotti sono immersi in vasche allineate per ricevere in sequenza lavorazioni di sgrassatura, ramatura, nichelatura e cromatura. È proprio l’ultima fase che conferisce, grazie all’aspetto estremamente brillante, un importante valore aggiunto al componente rendendolo un elemento distintivo delle macchine del caffè.
Pressofusione per il settore automotive: bloccasterzo elettronico
Nel video si presenta un componente automotive il cui stampo è stato progettato in modo anticonvenzionale e sul quale è stato applicato un sistema di filettatura automatica.
Questo componente del bloccasterzo elettronico ha richiesto una progettazione non convenzionale dello stampo perché è caratterizzato da una geometria complessa. Infatti, la sezione interna del prodotto, destinata ad accogliere una scheda elettronica e comprendente parti in scorrimento, ha determinato le principali difficoltà nella progettazione dello stampo. È stata quindi la complessità strutturale del componente, posta in relazione al processo di produzione, a determinare la necessità di ottenere un notevole livello di precisione in fase di mass production.
Dal momento che il prodotto è destinato a contenere al proprio interno una scheda elettronica ed ulteriori elementi funzionali è necessaria la totale assenza di difetti da pressofusione (come ad esempio le bave pendule) che potrebbero compromettere la funzionalità o del prodotto o degli elementi contenuti internamente. Per ottenere i livelli di precisione e di qualità richiesti lo stampo è stato perciò progettato con un approccio non convenzionale. La configurazione con la quale è stato progettato è infatti opposta a quella tradizionale: il pezzo viene prelevato dalla parte esterna, e non da quella interna come invece accade abitualmente. In questo modo si evitano sia la presenza di bave pendule sia gli estrattori nella parte interna del prodotto.
Dopo aver ottimizzato la progettazione dello stampo si è anche provveduto ad introdurre, nel ciclo di produzione, un sistema automatico di filettatura. È un sistema che, integrato nell’isola di stampaggio, consente sia la tranciatura della materozza sia la filettattura simultanea di due fori M8. Gli importanti benefici che derivano dall’implementazione di questo sistema sono due: innanzitutto si evitano lavorazioni manuali da parte dell’operatore (che è così libero di dedicarsi ad attività a maggior valore aggiunto) e, inoltre, si ottengono continuità ed efficienza produttiva, con il risparmio di costi e tempistiche che ne consegue. La tecnologia della pressofusione, e in particolare la pressofusione per bloccasterzo elettronico, grazie al nostro approccio innovativo e alle competenze tecniche dei nostri ingegneri, costituisce un’ottima scelta per la produzione di componenti automotive perché garantisce precisione realizzativa anche per i prodotti più complessi.
Pressofusione per il settore automotive: tetti panoramici
In questo video vi presentiamo un componente prodotto per il settore automotive caratterizzato da tolleranze molto ristrette e geometrie complesse.
Per questo pezzo, un componente dei tetti panoramici per autovetture che presenta una sagoma complessa e caratterizzata da zone molto sottili e difficili da ottenere, sono richiesti elevati livelli di accuratezza e precisone. Per raggiungere gli standard richiesti dal cliente sono state quindi adottate specifiche soluzioni tecniche che, assicurando la funzionalità del pezzo, hanno consentito di ottenere un prodotto privo di ogni minima deformazione.
L’implementazione delle soluzioni tecniche è stata attuata soprattutto in fase di progettazione dello stampo e di simulazione dei flussi di riempimento, mentre la progettazione del canale di alimentazione, dei carrelli e degli estrattori inclinati è stata curata nel dettaglio al fine di poter realizzare sagome complesse. Per la simulazione è stato adottato il software Magmasoft che ha consentito di ottimizzare i flussi di riempimento in tutto il pressofuso e soprattutto nelle zone più sottili: il risultato ottenuto è stato un riempimento uniforme ed omogeneo. Inoltre, per incrementare ancora di più la precisione del risultato è stato impiegato il sistema di stampaggio sotto vuoto: un tool progettato e realizzato in Bruschi al fine di evitare deviazioni dimensionali.
Le soluzioni tecniche ideate dai nostri ingegneri hanno così permesso di ottenere un prodotto conforme al nostro processo produttivo e caratterizzato da eccellenti proprietà tecniche in grado di incontrare la piena soddisfazione del cliente. Per l’industria automotive, e nel caso specifico per la produzione di componenti di tetti panoramici, la tecnologia della pressofusione permette quindi di ottenere componenti con tolleranze ristrette e sagome complesse che soddisfino appieno i rigidi standard del settore.
Pressofusione per porte e finestre: meccanismo di apertura
In questo video si mostra la produzione della custodia del meccanismo di apertura e chiusura per porte e finestre e se ne descrivono le caratteristiche funzionali ed estetiche.
Il componente fa parte del sistema di apertura di porte e finestre ed è quindi caratterizzato da proprietà funzionali ed estetiche. Le proprietà funzionali sono determinate dal fatto che il componente contiene al suo interno ulteriori elementi del meccanismo di apertura. Le proprietà estetiche, invece, derivano dalla sua natura di elemento esterno che entra in contatto con il cliente finale, per questa ragione il pezzo deve avere un’ottima qualità superficiale.
Pertanto, per la produzione e la progettazione di questo componente sono stati considerati aspetti molto diversi tra di loro e sono state trovate soluzioni in grado di assicurarne sia l’estetica che la funzionalità. Per quanto riguarda l’estetica si è mirato ad evitare la formazione di inclusioni d’aria nel pressofuso al fine di ottenere una superficie adatta alla verniciatura a polvere. La migliore qualità superficiale che si è ottenuta grazie a software di simulazione e alla valvola del vuoto ha permesso di ridurre gli scarti da verniciatura, passando da una percentuale di scarto di circa il 30% ad un valore vicino allo zero.
Per quanto riguarda la funzionalità, invece, è stata svolta, in collaborazione con il cliente, un’importante attività di re-design della parte interna del componente finalizzata al raggiungimento di spessori sottili che mantenessero inalterate le proprietà del prodotto. Gli spessori sottili, nel meccanismo di apertura di porte e finestre, sono importanti perché il componente contiene al suo interno il sistema di fissaggio e slittamento del meccanismo di apertura e la riduzione degli spessori ne incrementa la funzionalità. I vantaggi apportati dalla riduzione degli spessori sono notevoli e riguardano la minore quantità di materia prima utilizzata e la diminuzione del tempo ciclo di stampaggio. La produzione del componente, tuttavia, non si limita al processo di stampaggio: è stata infatti progettata e realizzata un’automazione per la filettatura di 6 fori M5, che avviene immediatamente dopo quella di stampaggio. Il prodotto passa attraverso un vibroburattatore e poi su una tavola rotante dotata di tre stazioni di filettatura. Il risultato dell’implementazione di questo sistema di filettatura automatica ha fatto sì che le tempistiche delle lavorazioni secondarie si riducessero notevolmente.
La pluriennale esperienza nella pressofusione per porte e finestre, le competenze tecniche e il know how hanno così reso possibile la produzione di un componente caratterizzato da specifiche proprietà estetiche e funzionali e capace di soddisfare le richieste del cliente.
Pressofusione per grandi elettrodomestici: cerniera per lavatrici
In questo video si descrive la produzione della cerniera per lavatrici e le soluzioni tecniche adottate per assicurare funzionalità al prodotto.
La cerniera per lavatrici è un componente funzionale del meccanismo di apertura dell’oblò dell’elettrodomestico. Questo elemento deve rispettare specifiche caratteristiche tecniche e deve soddisfare i requisiti di funzionalità richiesti dal cliente. È un prodotto caratterizzato da una sagoma particolarmente complessa che pone interessanti sfide in fase di progettazione e durante il processo produttivo.
Il rispetto delle richieste tecniche e funzionali del cliente, la necessità di conformare la realizzazione del pezzo al nostro processo produttivo e la complessità della forma del componente hanno richiesto un’attenta attività di progettazione che si è svolta in co-design con il cliente. Il co-design ci ha permesso di scambiare proficuamente informazioni ed esperienze, di realizzare uno stampo prototipale ad una cavità e di effettuare numerose verifiche funzionali e di affidabilità del processo. Tutte queste attività hanno portato all’ottimizzazione della sagoma della cerniera per lavatrici.
L’ottimizzazione della cerniera per lavatrici ha poi riguardato anche il processo produttivo. In questa fase è stata introdotta, a bordo macchina, un’automazione dedicata. L’automazione ha consentito di diminuire la presenza di difetti sul pressofuso dovuti alle lavorazioni e ha, di conseguenza, alleggerito il carico di lavoro degli operatori di reparto. In questo modo il lavoro a minor valore aggiunto è stato lasciato alla macchina e gli operatori si sono potuti dedicare ad attività a maggior valore aggiunto, come, ad esempio, il controllo qualità e il miglioramento dei processi produttivi, con evidenti benefici in termini di tempi e costi.
Infine, un’ultima implementazione è stata dedicata alla fase di assemblaggio. Abbiamo progettato e realizzato, in-house e ad hoc per il cliente, una macchina per l’assemblaggio semi automatico di boccole di plastica sui pressofusi in zama. Le cerniere sono disposte sulla macchina, comandata dal PLC, in diverse posizioni funzionali alla versione del prodotto che viene assemblato in uno specifico momento. La macchina, dotata di stazioni di carico, assemblaggio, controllo e scarico, rende il processo verticale ed è in grado di offrire un prodotto finito.
L’insieme di queste soluzioni (co-design, automazione a bordo macchina e assemblaggio semi automatico) hanno permesso di minimizzare il margine di errore, raggiungere la qualità richiesta dal cliente ed incrementare la sicurezza del processo di realizzazione della cerniera per lavatrici.