Marco Galbiati vince il “Premio Aldo Daccò 2020”
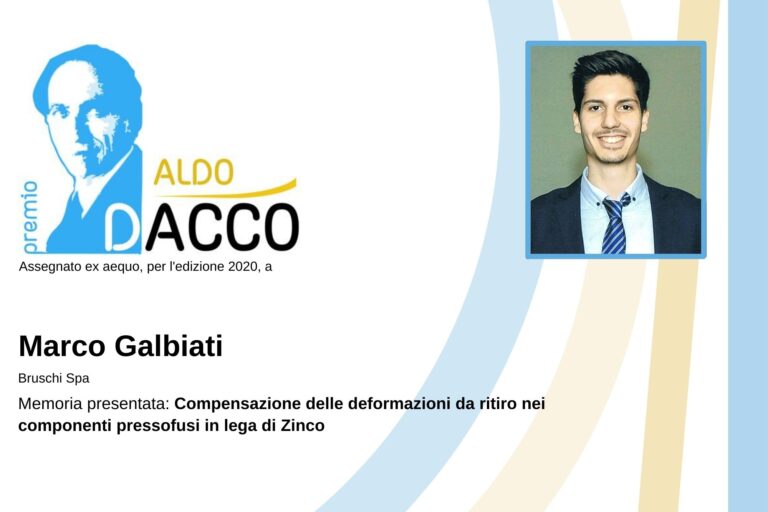
Bruschi è lieta di annunciare la premiazione del nostro collega Ing. Marco Galbiati, progettista meccanico presso Bruschi Spa, che in data 18 gennaio 2021 ha ricevuto il “Premio Aldo Daccò 2020”.
Anche quest’anno l’Associazione Italiana di Metallurgia (AIM) ha lanciato il bando per concorrere al “Premio Aldo Daccò 2020” edizione 2020, istituito nel 1975 per stimolare i tecnici del settore a contribuire allo sviluppo e al progresso delle tecniche di fonderia e di solidificazione attraverso la realizzazione di memorie e studi originali. La premiazione, visto il periodo, si è tenuta online il 18 gennaio 2021 in occasione della cerimonia di apertura del 38° Convegno Nazionale AIM.
L’edizione “Premio Aldo Daccò 2020” vede Marco come vincitore ex aequo, insieme all’Ing. Lavinia Tonelli, che ha partecipato al bando presentando l’elaborato scientifico dal titolo: “Compensazione delle deformazioni da ritiro nei componenti pressofusi in lega di zinco”.
L’abbiamo dunque intervistato per farci raccontare il contenuto del suo elaborato e complimentarci con lui per il grande risultato ottenuto.
Parlaci del concorso a cui hai partecipato, di cosa si tratta e come mai hai deciso di gareggiare?
L’AIM è un ente culturale, senza fini di lucro, fondato nel gennaio 1946 che ha come obiettivo diffondere la scienza e la tecnologia dei materiali metallici ed altri materiali per l’ingegneria. Nel solco della sua missione l’AIM da 45 anni organizza questo concorso che, personalmente, seguo da sempre e a cui mi sarebbe sempre piaciuto partecipare. Collaborando in questi anni presso Bruschi Spa ho deciso di combinare le mie conoscenze tecniche e l’esperienza sviluppata sul campo per fornire il mio contributo allo sviluppo e all’approfondimento delle conoscenze delle tecniche di fonderia e solidificazione.
Di cosa parla l’elaborato scientifico che hai sottoposto per la partecipazione al concorso?
L’elaborato scientifico presentato si intitola: “Compensazione delle deformazioni da ritiro nei componenti pressofusi in lega di zinco”. In particolare, esso si focalizza su una specifica criticità dei pressofusi in lega di zinco: il verificarsi di deformazioni dei prodotti causate dal ritiro di materiale nella fase successiva allo stampaggio. Nell’elaborato ho fatto emergere le difficoltà riscontrate e i possibili metodi di risoluzione di tale problematica.
Come mai hai deciso di sviluppare proprio questa tematica?
Le problematiche trattate nel mio elaborato sono emerse durante l’ispezione di particolari prodotti presso la Bruschi Spa. Queste problematiche sono state inizialmente scoperte dal Quality Engineer Andrea Salmistraro che, durante la fase di analisi dei componenti attraverso l’utilizzo di uno scanner 3D, ha notato che alcune importanti quote venivano alterate da un difetto dovuto alla deformazione della lega. Grazie al coinvolgimento e al contributo del nostro Strategic Technology Manager Ermo Fusè abbiamo ipotizzato e successivamente dimostrato che tale difetto fosse correlato al ritiro di solidificazione della Zamak, che si presenta con entità variabile a seconda della distribuzione della massa nel componente. Col mio elaborato ho dunque voluto dimostrare che è possibile contrastare le deformazioni da ritiro di materiale esponendo la soluzione da noi individuata.
Come sei riuscito a trovare la soluzione?
Il primo passo è stato verificare che lo stampo non avesse alterazioni che potessero ricondurre a questa problematica. Una volta accertata l’idoneità di matrici e carrelli sono stati analizzati due casi pratici in cui i componenti, pur avendo caratteristiche geometriche nettamente differenti, presentavano la medesima problematica:
- Deformazione di superficie piana: in questo caso siamo partiti dalla scansione del pezzo deformato. Questa ci ha permesso di estrapolare, grazie a un software a CAD, un reticolo con il quale ho ricostruito digitalmente la superficie deformata per poi simmetrizzarla in modo da ottenere una superficie contro-deformata. Abbiamo infine applicato questa superficie alla corrispondente parte stampante in modo da ottenere un pezzo deformato nel verso opposto che sarebbe risultato conforme una volta raffreddatosi.
- Deformazione su superficie cilindrica: per questo caso abbiamo seguito un procedimento simile al precedente, con l’unica eccezione che non è stato possibile replicare e simmetrizzare la superficie deformata per via della complessità della geometria. Abbiamo quindi individuato le zone deformate grazie alla scansione e, dopo averle delimitate con il software CAD, le abbiamo proiettate direttamente sulle parti stampanti andando, poi, a contro-deformarle.
Nell’elaborato emerge che le deformazioni trattate sono dell’ordine dei decimi ma anche dei centesimi di millimetro, come siete riusciti a garantire l’adeguata accuratezza di lavorazione?
L’attrezzista e programmatore CAM Matteo Annovazzi, grazie ai suoi numerosi anni di esperienza e alla profonda conoscenza delle attrezzature, è riuscito a replicare fedelmente quanto progettato realizzando un accurato programma CAM per il controllo della fresatrice con cui ha poi lavorato le parti stampanti.
Cosa pensi di questa esperienza e della vittoria portata a casa?
Sono molto soddisfatto del risultato ottenuto. Sono orgoglioso dell’esistenza di enti che si impegnano per promuovere lo sviluppo, lo scambio di idee e diffondere le conoscenze relative a questo settore. Vorrei inoltre ringraziare la Bruschi Spa per avermi permesso di svolgere gli studi esposti in questo elaborato e il supporto ricevuto dall’intero team. È proprio grazie alla collaborazione dei diversi ingegneri e tecnici del team Bruschi che sono riuscito a dimostrare che è possibile contrastare le deformazioni da ritiro di materiale mediante una contro-deformazione volontaria e mirata delle parti stampanti che generano le superfici interessate da questa problematica. Non è una mia vittoria ma è una vittoria della squadra.